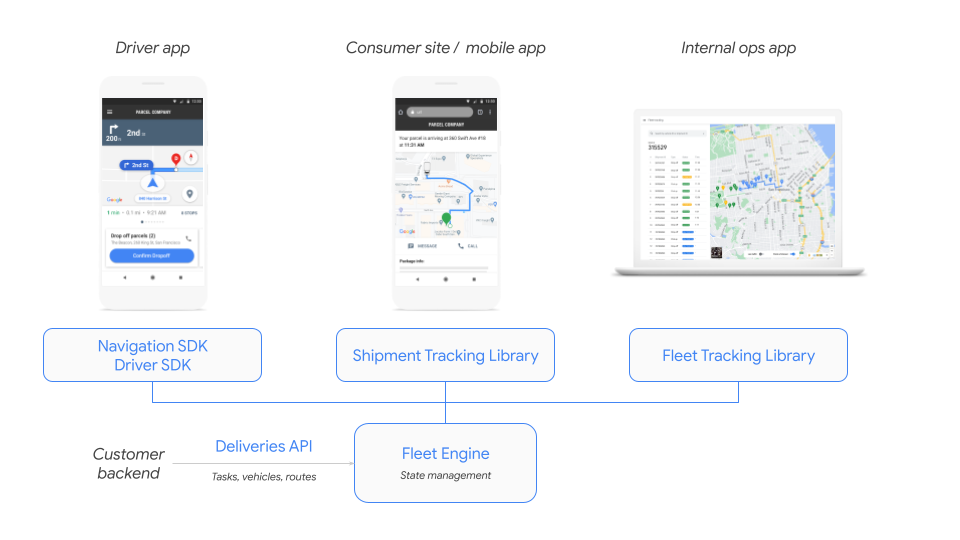
A business case can prove to be an important tool for anyone involved in a project. It is a document which outlines the benefits and cost of a project. It is often used by decision-makers to decide which projects they should take on. It can also be used to evaluate project success.
To prepare a business case, it is important to identify the interdependencies between the project's components and those of related projects. This will help ensure that the project addresses the right problem and solves the right problem. The brief outline should include the expected time frame and major deliverables.
Next, you need to identify the resources required to complete the business case. This should include financial resources, intellectual and physical resources. Include information about who will be working on the project. It is essential that everyone involved has the right skills to execute the project.
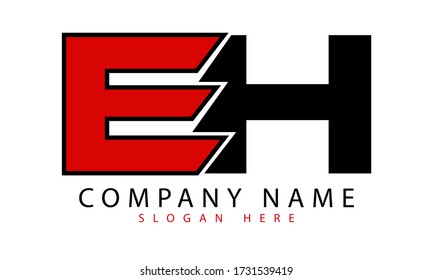
After you have determined the resources needed to complete the project, the next step is to create a risk assessment. These should include both external and internal risks. It is also important to sketch the probability of these risks occurring. These risks must be compared with the benefits of a project. The external environment may change the project's potential benefits. A project's inherent risks should be considered.
Next, describe the benefits of your project. This will help convince stakeholders that your project is worthwhile. It should also include details of the procurement strategy, implementation approach, and sustainability practices that you are going to adopt.
Projects often start without context. It is important to provide the project sponsor with a clear picture of the project, the key benefits of the project, and the risks associated with the project. It is important to clearly define the responsibility of the project.
The final step in preparing a business case is the presentation of the document to stakeholders. This can include the project sponsor, finance function, and project team. The sponsor will typically approve the business case. The document may also be reviewed by other interested parties.
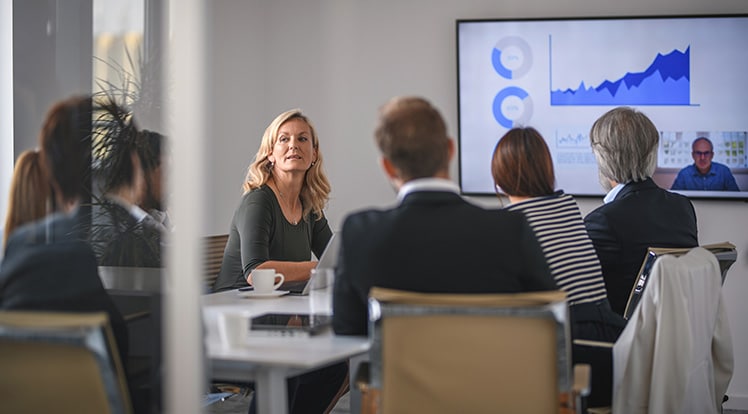
Once the business plan has been approved, you will be able to begin to create the implementation plan. This document will outline the project team, milestones and costs, as well as details about risks and milestones. This should list the main benefits of the project as well as the reasons you feel the project should be continued. You should also detail the benefits of the project's sustainability practices.
The business case is not just a useful tool for decision-making but it should be used consistently. It can help you determine which projects are most important to achieve your goals.
FAQ
What are the four major functions of Management?
Management is responsible in planning, organizing and directing people and resources. It includes creating policies and procedures, as well setting goals.
Management assists an organization in achieving its goals by providing direction, coordination and control, leadership, motivation, supervision and training, as well as evaluation.
The four main functions of management are:
Planning - Planning refers to deciding what is needed.
Organizing - Organization involves deciding what should be done.
Direction - This is the art of getting people to follow your instructions.
Controlling: Controlling refers to making sure that people do what they are supposed to.
What is the role of a manager in a company?
Different industries have different roles for managers.
Managers generally oversee the day-today operations of a business.
He/she ensures the company meets its financial commitments and produces goods/services that customers demand.
He/she ensures employees adhere to all regulations and quality standards.
He/she designs new products or services and manages marketing campaigns.
How can a manager improve his/her managerial skills?
Through demonstrating good management skills at every opportunity
Managers should monitor the performance and progress of their subordinates.
It is important to take immediate action if your subordinate doesn't perform as expected.
You should be able pinpoint what needs to improve and how to fix it.
How can we create a successful company culture?
A positive company culture creates a sense of belonging and respect in its people.
It is founded on three basic principles:
-
Everybody can contribute something valuable
-
People are treated fairly
-
Individuals and groups can have mutual respect
These values reflect in how people behave. For example, they will treat others with courtesy and consideration.
They will respect the opinions of others.
They encourage others to express their feelings and ideas.
Additionally, the company culture encourages open communication as well as collaboration.
People feel free to express their views openly without fear of reprisal.
They are aware that mistakes can be accepted if they are treated honestly.
The company culture encourages honesty and integrity.
Everyone knows that they must always tell truth.
Everyone is aware that rules and regulations apply to them.
People don't expect special treatment or favors.
Statistics
- The BLS says that financial services jobs like banking are expected to grow 4% by 2030, about as fast as the national average. (wgu.edu)
- Our program is 100% engineered for your success. (online.uc.edu)
- This field is expected to grow about 7% by 2028, a bit faster than the national average for job growth. (wgu.edu)
- The average salary for financial advisors in 2021 is around $60,000 per year, with the top 10% of the profession making more than $111,000 per year. (wgu.edu)
- 100% of the courses are offered online, and no campus visits are required — a big time-saver for you. (online.uc.edu)
External Links
How To
What is Lean Manufacturing?
Lean Manufacturing techniques are used to reduce waste while increasing efficiency by using structured methods. They were developed by Toyota Motor Corporation in Japan during the 1980s. The aim was to produce better quality products at lower costs. Lean manufacturing is about eliminating redundant steps and activities from the manufacturing process. It consists of five basic elements: pull systems, continuous improvement, just-in-time, kaizen (continuous change), and 5S. Pull systems allow customers to get exactly what they want without having to do extra work. Continuous improvement involves constantly improving upon existing processes. Just-in-time is when components and other materials are delivered at their destination in a timely manner. Kaizen refers to continuous improvement. It is achieved through small changes that are made continuously. Five-S stands for sort. It is also the acronym for shine, standardize (standardize), and sustain. These five elements are combined to give you the best possible results.
Lean Production System
The lean production system is based on six key concepts:
-
Flow - The focus is on moving information and material as close as possible to customers.
-
Value stream mapping is the ability to divide a process into smaller tasks, and then create a flowchart that shows the entire process.
-
Five S's: Sort, Shine Standardize, Sustain, Set In Order, Shine and Shine
-
Kanban - use visual signals such as colored tape, stickers, or other visual cues to keep track of inventory;
-
Theory of constraints - identify bottlenecks in the process and eliminate them using lean tools like kanban boards;
-
Just-in-time delivery - Deliver components and materials right to your point of use.
-
Continuous improvement: Make incremental improvements to the process instead of overhauling it completely.