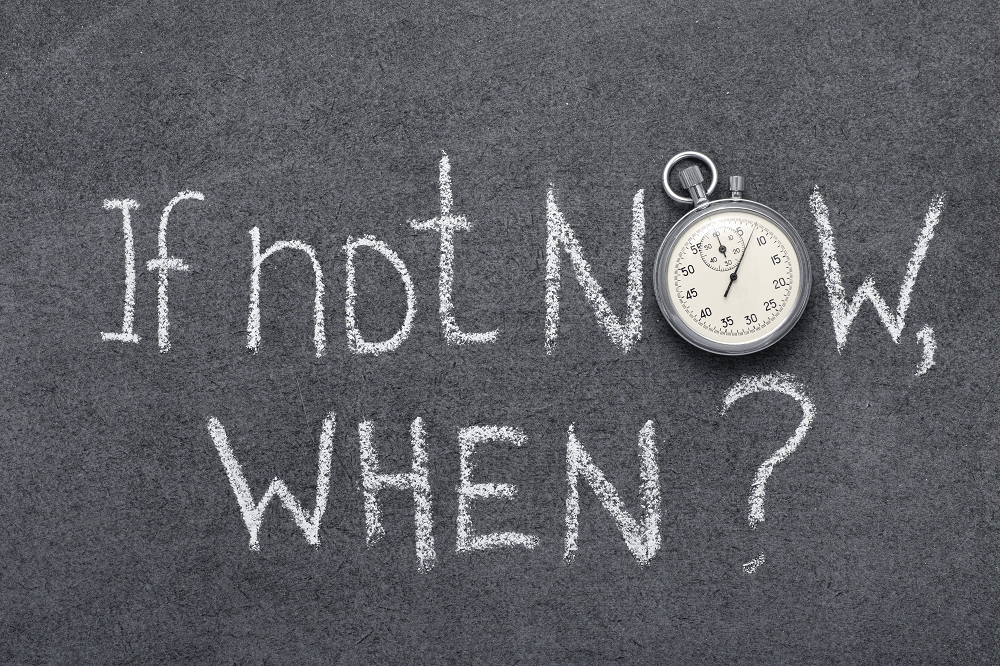
For the purpose of transforming an old building into a new one, it's advisable to hire professional turner contractor. But you need to be aware of both the costs and the benefits of hiring a professional. Here are some reasons why you might want to hire turner contract workers. Keep reading to learn more. It is possible to have a professional finish your building. Find out the cost and benefits of hiring an experienced contractor.
Professional turner contractors
A professional contractor is available for any home renovation or major addition. With a focus on quality workmanship and exceptional customer service, you can trust Turner Contracting to create a home that's both functional and beautiful. They provide quality home remodeling services throughout West Central Florida and are ready to help you turn your remodeling dreams into reality. Learn more about Turner's services.
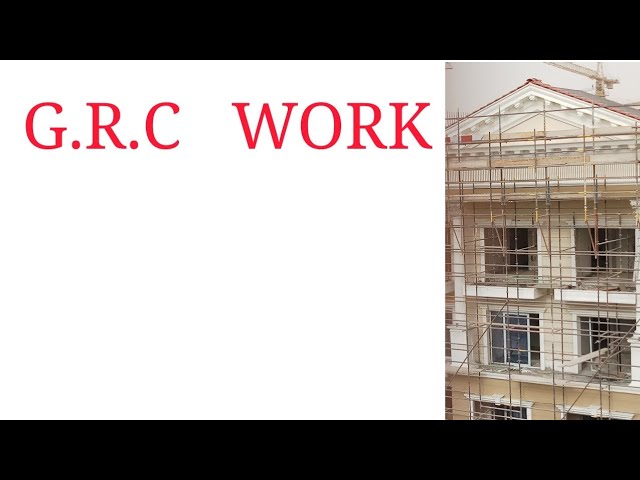
The Turner Construction Company is an international construction company based in the United States. It employs approximately 5000 people, and it completes more than 1,500 building projects annually. This company is known as the pioneer in steel-reinforced concreting, which can be used to make safer, stronger and more energy-efficient buildings. The company uses the ingenuity and creativity of its employees to create new structures. The company's headquarters are located in New York City. The company website has a number of contact information. Sumele also maintains a blog about architecture. She loves to read and cook.
Costs for hiring professional turner contractor
If you're looking for a general contract, it's a smart move to choose a company that specializes only in turner construction. This company is able to handle large-scale projects and will provide high quality work. Additionally, they will likely offer more competitive rates and have no hidden fees. Whether you're looking for a general contractor in the Philadelphia area or in another state, there are many options available.
Hiring professional turner contractors has many benefits
If you're looking for a contractor to do a job on your home, you may want to consider working with a Turner contractor. The contractors provide a variety of benefits for their employees. These benefits include federal holiday pay, 401k matching and 10 sick day. They also offer health coverage and vision insurance. They also offer generous PTO. They offer support to employees who start a family.
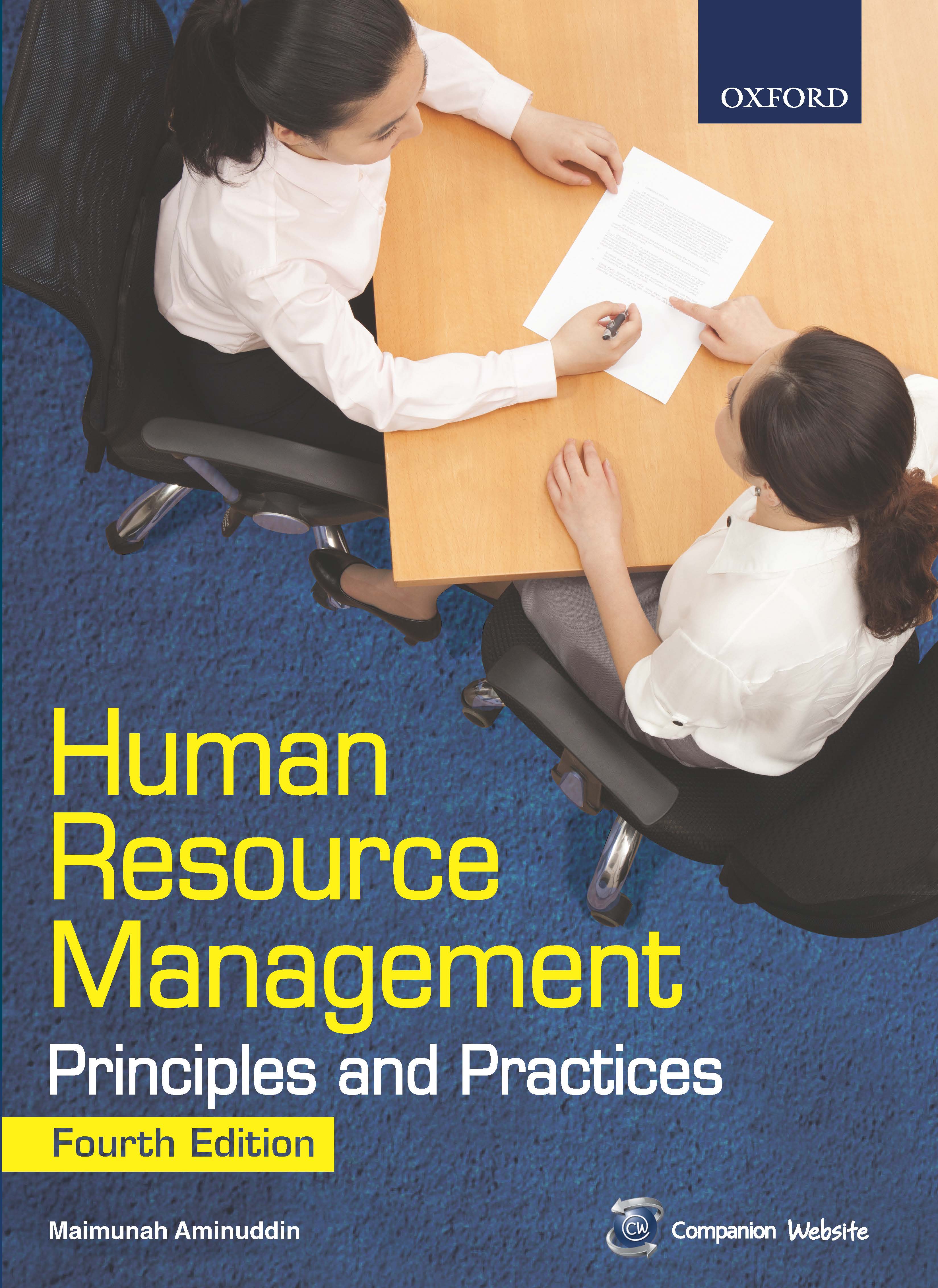
Multiple projects are managed by the C-suite. They also make sure to adhere to ethics and policies regarding contract negotiation. In addition, they oversee the financial management of all projects. Turner is a large corporation, so their project managers are often involved in multiple projects at once. These managers have many duties and are responsible in maintaining a positive attitude, and keeping the company's track.
FAQ
How to effectively manage employees
Effectively managing employees requires that you ensure their happiness and productivity.
It means setting clear expectations for them and keeping an eye on their performance.
Managers need clear goals to be able to accomplish this.
They should communicate clearly to staff members. And they need to ensure that they reward good performance and discipline poor performers.
They should also keep records of all activities within their team. These include:
-
What did we accomplish?
-
How much work did you put in?
-
Who did it?
-
It was done!
-
Why did it happen?
This information can be used to monitor performance and evaluate results.
What are the 3 main management styles?
These are the three most common management styles: participative (authoritarian), laissez-faire (leavez-faire), and authoritarian. Each style has its strengths and weaknesses. Which style do your prefer? Why?
Authority - The leader is the one who sets the direction and expects everyone in the organization to follow it. This style is best when the organization has a large and stable workforce.
Laissez faire - Each individual can decide for himself/herself. This style works best when an organization is small and dynamic.
Participative - Leaders listen to all ideas and suggestions. This approach works best in small organizations where everyone feels valued.
What are management concepts, you ask?
Management concepts are the fundamental principles and practices that managers use when managing people and their resources. They cover topics like job descriptions (job descriptions), performance evaluations, training programmes, employee motivation and compensation systems.
Why does it sometimes seem so difficult to make good business decisions?
Complex systems with many moving parts are the hallmark of businesses. The people who run them must juggle multiple priorities at once while also dealing with uncertainty and complexity.
Understanding how these factors impact the whole system is key to making informed decisions.
You must first consider what each piece of the system does and why. You then need to consider how those individual pieces interact with each other.
Also, you should ask yourself if there have been any assumptions in your past behavior. If they don't, you may want to reconsider them.
Asking for assistance from someone else is a good idea if you are still having trouble. They might see things differently than you and may have some insights that could help find a solution.
Why is project management so important?
Project management techniques can be used to ensure smooth project execution and meeting deadlines.
Because most businesses depend heavily on project work to produce goods or services,
These projects must be managed efficiently and effectively by companies.
Without effective project management, companies may lose money, time, and reputation.
What is TQM?
The quality movement was born during the industrial revolution when manufacturing companies realized they could not compete on price alone. They needed to improve the quality and efficiency of their products if they were to be competitive.
Management responded to the need to improve, and developed Total Quality Management (TQM). This focused on improving every aspect of an organization’s performance. It involved continuous improvement, employee participation, and customer satisfaction.
What is the difference in Six Sigma and TQM?
The main difference between these two quality-management tools is that six-sigma concentrates on eliminating defects while total QM (TQM), focuses upon improving processes and reducing expenses.
Six Sigma is an approach for continuous improvement. It emphasizes the elimination and improvement of defects using statistical methods, such as control charts, P-charts and Pareto analysis.
This method has the goal to reduce variation of product output. This is done by identifying root causes and rectifying them.
Total Quality Management involves monitoring and measuring every aspect of the organization. It also involves training employees to improve performance.
It is often used to increase productivity.
Statistics
- Hire the top business lawyers and save up to 60% on legal fees (upcounsel.com)
- Your choice in Step 5 may very likely be the same or similar to the alternative you placed at the top of your list at the end of Step 4. (umassd.edu)
- Our program is 100% engineered for your success. (online.uc.edu)
- The profession is expected to grow 7% by 2028, a bit faster than the national average. (wgu.edu)
- 100% of the courses are offered online, and no campus visits are required — a big time-saver for you. (online.uc.edu)
External Links
How To
What is Lean Manufacturing?
Lean Manufacturing methods are used to reduce waste through structured processes. They were created in Japan by Toyota Motor Corporation during the 1980s. The goal was to produce quality products at lower cost. Lean manufacturing is about eliminating redundant steps and activities from the manufacturing process. It is made up of five elements: continuous improvement, continuous improvement, just in-time, continuous change, and 5S. It is a system that produces only the product the customer requests without additional work. Continuous improvement refers to continuously improving existing processes. Just-intime refers the time components and materials arrive at the exact place where they are needed. Kaizen is continuous improvement. This can be achieved by making small, incremental changes every day. Finally, 5S stands for sort, set in order, shine, standardize, and sustain. These five elements are used together to ensure the best possible results.
The Lean Production System
Six key concepts underlie the lean production system.
-
Flow is about moving material and information as near as customers can.
-
Value stream mapping: This is a way to break down each stage into separate tasks and create a flowchart for the entire process.
-
Five S's – Sort, Put In Order Shine, Standardize and Sustain
-
Kanban: Use visual signals such stickers, colored tape, or any other visual cues, to keep track your inventory.
-
Theory of constraints - identify bottlenecks during the process and eliminate them with lean tools like Kanban boards.
-
Just-in-time delivery - Deliver components and materials right to your point of use.
-
Continuous improvement - make incremental improvements to the process rather than overhauling it all at once.