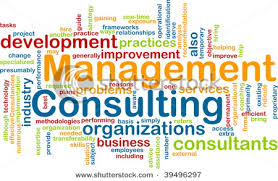
You don't matter whether you're in business for big or small profits, you need to learn how to create and implement a communication plan that works. The art of managing a communication plan is itself an art. If you're in the throes of a new project or rebranding, you'll want to make sure your communication plan is in place to avoid an expensive hiccup down the road. A solid communication strategy will help your business grow without any risk.
While you're at it, you'll want to consider how you're going to manage your communications budget. A budget should allow you to make the most of opportunities, avoid pitfalls, meet your financial obligations, and take advantage of them. The budget you select should be high enough to ensure the growth of your business without compromising your financial well being.
The right mix of media and tactics is key to creating a great communication plan. The key to a good communication plan is to understand your target audience and identify areas where you can improve upon what you already do. It is important to consider the right people and tools in order to ensure that information flows smoothly. It's also important to assess the impact of your communication strategy and to make necessary adjustments.
A discussion with key stakeholders is the best way of determining what works well. Consult a consultant to help you decide which communication tools work best for your team. This can be done by asking your key employees what types of communication tools they prefer and why. You should then incorporate these ideas into your communications plan. To avoid making a mistake, you will want to develop a communication strategy that follows best practices.
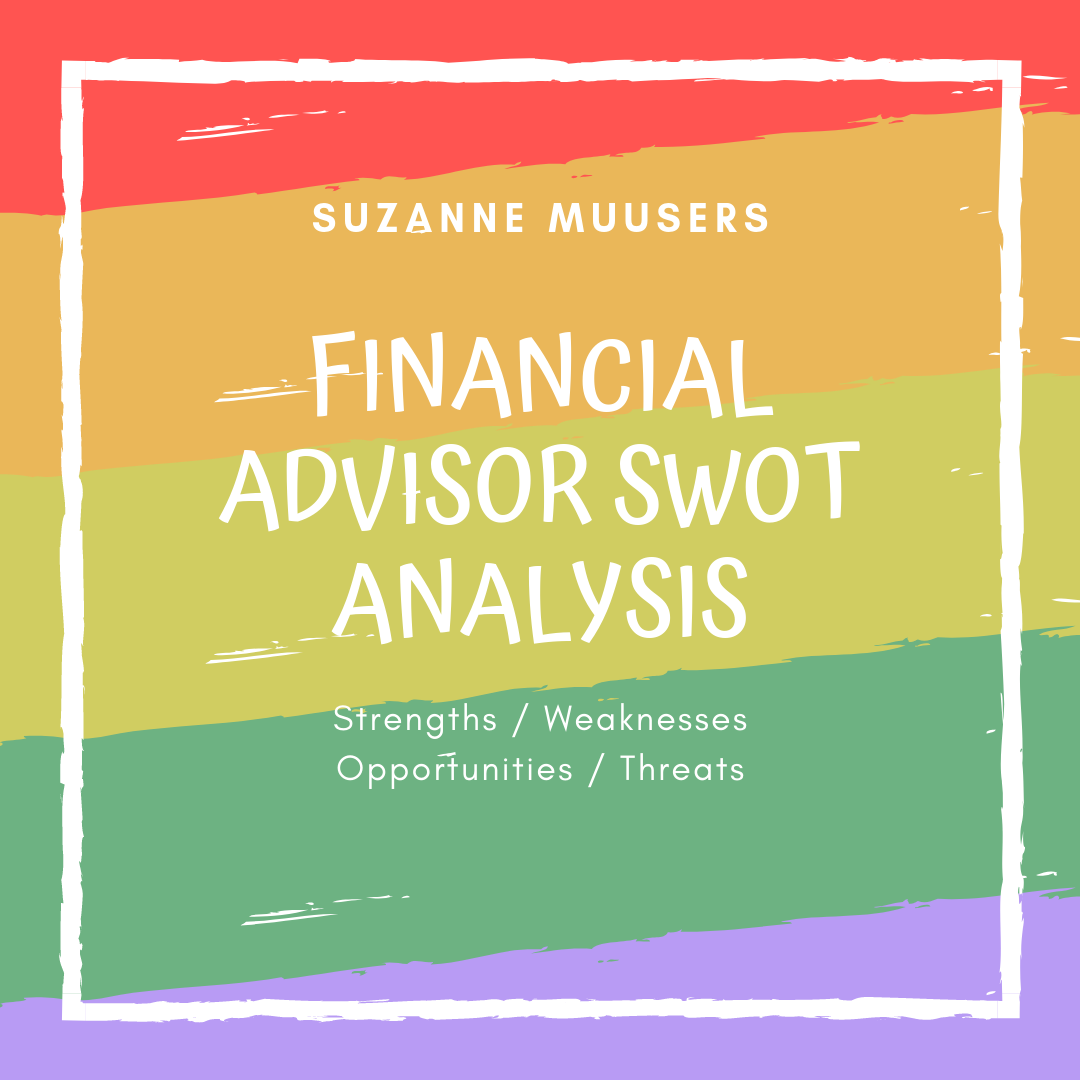
The best communication plan is one that is well thought out and tested. For example, you may want to include the top communications priorities in your budget so you know where to focus your efforts. It's also a good idea, as mentioned earlier, to evaluate the cost of implementing actions to ensure you're getting the best value for your dollar. It's also a good idea, especially if you're planning on expanding your business, to create a communications budget that can be adjusted as your business grows and changes.
FAQ
What is the main difference between Six Sigma Six Sigma TQM and Six Sigma Six Sigma?
The major difference between the two tools for quality management is that six Sigma focuses on eliminating defect while total quality control (TQM), on improving processes and decreasing costs.
Six Sigma stands for continuous improvement. This method emphasizes eliminating defects using statistical methods such p-charts, control charts, and Pareto analysis.
This method seeks to decrease variation in product output. This is accomplished by identifying the root cause of problems and fixing them.
Total quality management involves measuring and monitoring all aspects of the organization. Training employees is also part of total quality management.
It is often used to increase productivity.
Why is it important for companies to use project management techniques?
Project management techniques are used to ensure that projects run smoothly and meet deadlines.
This is due to the fact that most businesses rely heavily upon project work in order to produce goods, and services.
These projects are essential for companies.
Companies may lose their reputation, time and money if they do not have effective project management.
What does Six Sigma mean?
Six Sigma uses statistical analysis to find problems, measure them, analyze root causes, correct problems, and learn from experience.
The first step in solving a problem is to identify it.
Next, data is collected and analyzed to identify trends and patterns.
Then, corrective actions can be taken to resolve the problem.
The data are then reanalyzed to see if the problem is solved.
This cycle continues until the problem is solved.
Statistics
- Our program is 100% engineered for your success. (online.uc.edu)
- This field is expected to grow about 7% by 2028, a bit faster than the national average for job growth. (wgu.edu)
- As of 2020, personal bankers or tellers make an average of $32,620 per year, according to the BLS. (wgu.edu)
- The profession is expected to grow 7% by 2028, a bit faster than the national average. (wgu.edu)
- Your choice in Step 5 may very likely be the same or similar to the alternative you placed at the top of your list at the end of Step 4. (umassd.edu)
External Links
How To
How can you implement the Kaizen technique?
Kaizen means continuous improvement. The term was coined in the 1950s at Toyota Motor Corporation and refers to the Japanese philosophy emphasizing constant improvement through small incremental changes. It's where people work together in order to improve their processes constantly.
Kaizen, a Lean Manufacturing method, is one of its most powerful. This concept requires employees to identify and solve problems during manufacturing before they become major issues. This way, the quality of products increases, and the cost decreases.
Kaizen is a way to raise awareness about what's happening around you. It is important to correct any problems immediately if they are discovered. So, if someone notices a problem while working, he/she should report it to his/her manager.
Kaizen is based on a few principles. We always start from the end product and move toward the beginning. In order to improve our factory's production, we must first fix the machines producing the final product. Next, we fix the machines which produce components. We then fix the workers that work with those machines.
This method, called 'kaizen', focuses on improving each and every step of the process. We finish fixing the factory and then go back to the beginning. This continues until we achieve perfection.
It is important to understand how to measure the effectiveness and implementation of kaizen in your company. There are several ways that you can tell if your kaizen system is working. Another method is to see how many defects are found on the products. Another way is to see how much productivity has increased since implementing kaizen.
Another way to know whether kaizen is working is to ask yourself why did you decide to implement kaizen. It was because of the law, or simply because you wanted to save some money. It was a way to save money or help you succeed.
Congratulations! Now you're ready for kaizen.