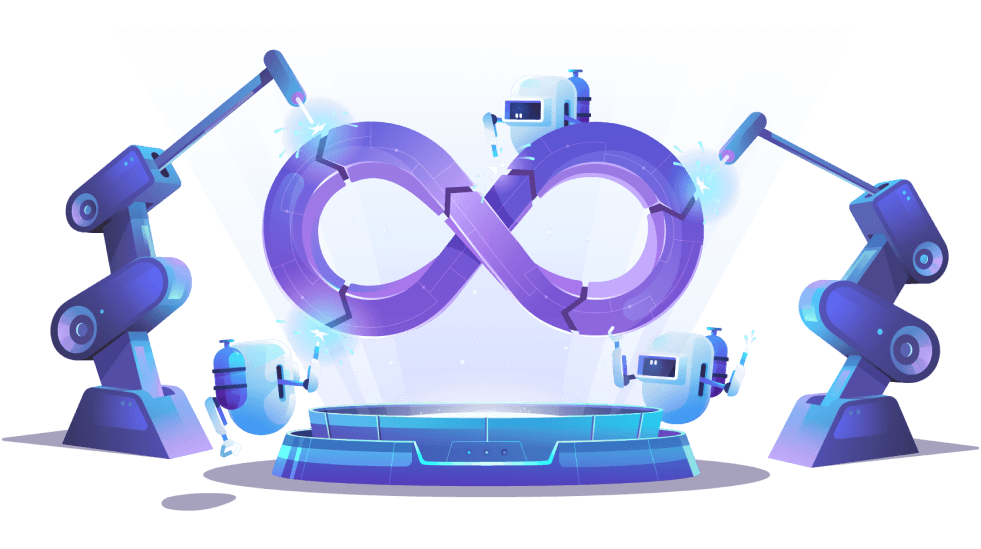
This book will provide you with a practical and strategic strategy for managing global supply chains. This book presents a systematic, comprehensive and easy to understand content that will be helpful for practitioners and researchers. Highly recommended. This book explains key concepts and the processes involved in strategic supply chain management. The authors provide a step by step guide to achieving strategic supply chains objectives. This book is highly recommended by both researchers and practitioners.
Demand-driven supply chains
A demand-driven supply chain is a strategic supply chain in which the entire chain responds to changes in demand. This allows companies to anticipate customer demands and meet them immediately. It is different than the traditional model in which the supplier announces that a new product is available and then the retailer takes delivery. This model allows companies control of their inventories and improves efficiency. Demand-driven supply chains allow companies to respond faster and more efficiently to customer needs.
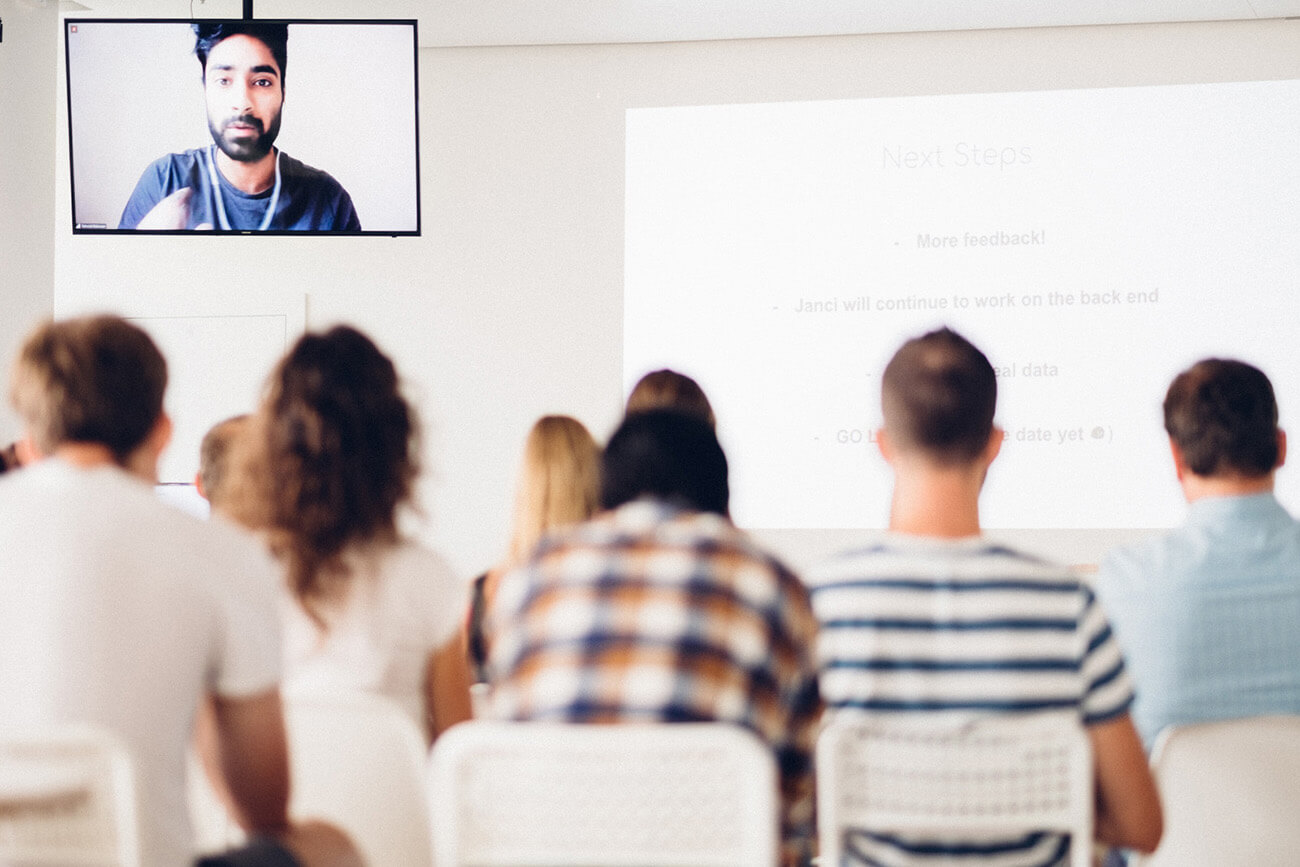
Planning
To optimize and plan the supply chain, tools that are organization-based are used. These planning approaches support different types of decision-making. An annual strategic business plan is essential to ensure a company's success and to identify growth opportunities. Supply chain planning software is used by many organizations to plan and optimize their supply networks. Here are some examples of different planning approaches. You can choose which one you prefer based on your preferred planning process.
Execution
Strategic supply chain management is the formal approach to managing the supply chain network of an organization. A supply chain manager creates a strategy that maximizes value, efficiency, resilience. It must align with the company's overarching business strategy. Effective supply chain management requires meticulous planning and execution. Understanding your supply chain is key to your business strategy. Here are some tips for successful supply chain management. Establish a vision for your supply chains.
Monitoring
Effective management depends on information. Ineffective management is possible when managers lack the data and tools needed to make informed decisions. As supply chain complexity increases, managers who neglect to monitor it are not equipped to handle potential disruptions. This is why supply chain monitoring is essential. There are many benefits to monitoring the supply chain. Here are just few. Read on to find out how to get started.
Sustainability
It is difficult to achieve true sustainability in a strategic supply network. It's more difficult to achieve true sustainability in a complex supply chain. Therefore, the procurement team should designate a sustainability point person to lead the sustainability process and regularly assess the progress of main suppliers. The procurement team should also create sustainability goals for suppliers and force them to achieve these goals. This will ensure transparency throughout the whole process. One way to measure supplier performance effectively is to measure the number or services that contribute to the company’s sustainability goals.
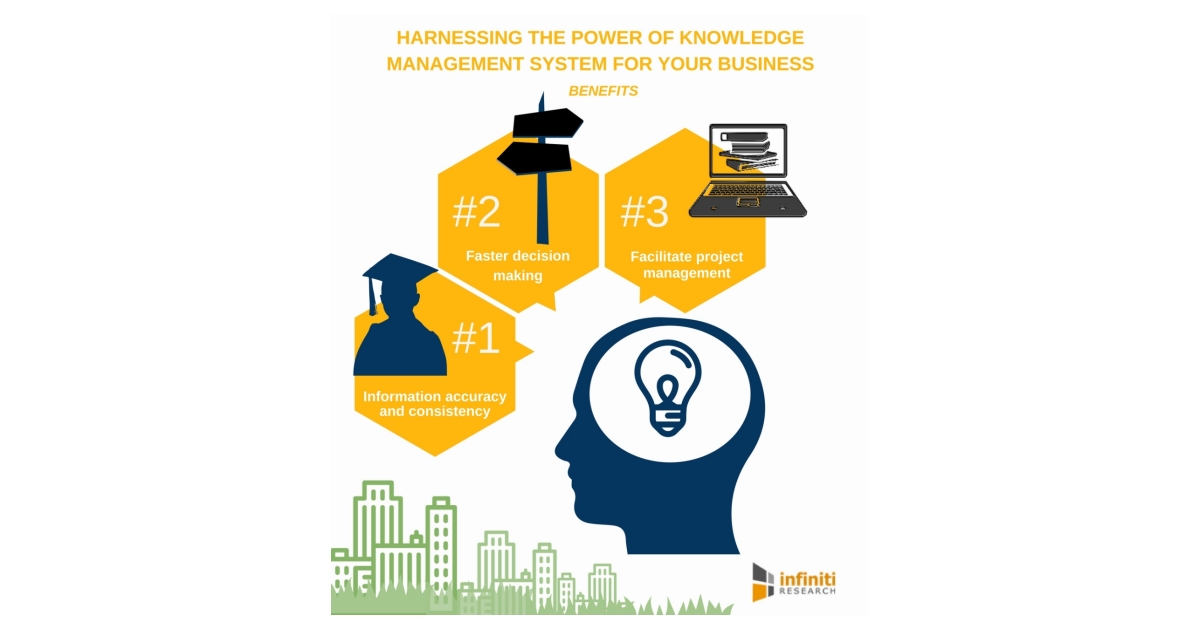
Variations depending on the product type
Companies should offer a broad range of products to consumers in order to maximize their performance. Companies often launch product variations and do not know if these will complicate their supply chains. In fact, consumer-goods companies have increased their number of products each year by 60% between 2002 and 2011. While the demand for these products increased, so did their costs. For example, U.S. consumer goods companies increased their annual number of new products by 60 percent during the same period. Although this inevitably led to an increase in costs across many parts of the supply chain, it was steady at only 2.8 per year.
FAQ
What is Six Sigma?
This is a method of quality improvement that emphasizes customer service, continuous learning, and customer service. The objective is to eliminate all defects through statistical methods.
Motorola's 1986 efforts to improve manufacturing process efficiency led to the creation of Six Sigma.
The idea quickly spread in the industry. Many organizations today use six-sigma methods to improve product design and production, delivery and customer service.
How to effectively manage employees
Managing employees effectively means ensuring that they are happy and productive.
It also means having clear expectations of their behavior and keeping track of their performance.
To do this successfully, managers need to set clear goals for themselves and for their teams.
They must communicate clearly with their staff. And they need to ensure that they reward good performance and discipline poor performers.
They should also keep records of all activities within their team. These include:
-
What did you accomplish?
-
How much work was put in?
-
Who did it all?
-
What was the moment it was completed?
-
Why it was done?
This information can be used for monitoring performance and evaluating results.
What are the five management steps?
The five stages of a business include planning, execution (monitoring), review, evaluation, and review.
Planning means setting goals for the long-term. Planning involves defining your goals and how to get there.
Execution is when you actually execute the plans. You need to make sure they're followed by everyone involved.
Monitoring is checking on progress towards achieving your objectives. Regular reviews of performance against budgets and targets should be part of this process.
Each year, reviews are held at the end. These reviews allow you to evaluate whether the year was successful. If not there are changes that can be made to improve the performance next year.
Evaluation takes place after the annual review. It helps identify which aspects worked well and which didn't. It also gives feedback on how well people did.
What are some common management mistakes?
Sometimes managers make it harder for their employees than is necessary.
They might not give enough support and delegate the right responsibilities to their staff.
A majority of managers lack the communication skills needed to motivate their team and lead them.
Managers set unrealistic expectations and make it difficult for their team.
Managers might try to solve every problem by themselves rather than delegating the responsibility.
Statistics
- Your choice in Step 5 may very likely be the same or similar to the alternative you placed at the top of your list at the end of Step 4. (umassd.edu)
- Hire the top business lawyers and save up to 60% on legal fees (upcounsel.com)
- The profession is expected to grow 7% by 2028, a bit faster than the national average. (wgu.edu)
- The average salary for financial advisors in 2021 is around $60,000 per year, with the top 10% of the profession making more than $111,000 per year. (wgu.edu)
- As of 2020, personal bankers or tellers make an average of $32,620 per year, according to the BLS. (wgu.edu)
External Links
How To
How do you apply the Kaizen method to your life?
Kaizen means continuous improvement. Kaizen is a Japanese concept that encourages constant improvement by small incremental changes. It's a process where people work together to improve their processes continuously.
Kaizen is one of Lean Manufacturing's most efficient methods. In this concept, employees who are responsible for the production line must identify problems that exist during the manufacturing process and try to solve them before they become big issues. This improves the quality of products, while reducing the cost.
Kaizen is an approach to making every worker aware and alert to what is happening around them. Correct any errors immediately to avoid future problems. If someone is aware of a problem at work, he/she should inform his/her manager immediately.
Kaizen has a set of basic principles that we all follow. Start with the end product, and then move to the beginning. If we want to improve our factory for example, we start by fixing the machines that make the final product. We then fix the machines producing components, and the machines producing raw materials. We then fix the workers that work with those machines.
This method is known as kaizen because it focuses upon improving every aspect of the process step by step. We finish fixing the factory and then go back to the beginning. This continues until we achieve perfection.
Before you can implement kaizen into your business, it is necessary to learn how to measure its effectiveness. There are several ways to determine whether kaizen is working well. One of these ways is to check the number of defects found on the finished products. Another way to find out how productive your company has been since you implemented kaizen is to measure the increase in productivity.
If you want to find out if your kaizen is actually working, ask yourself why. You were trying to save money or obey the law? Did you really believe that it would be a success factor?
Suppose you answered yes to any of these questions, congratulations! You are ready to start kaizen.