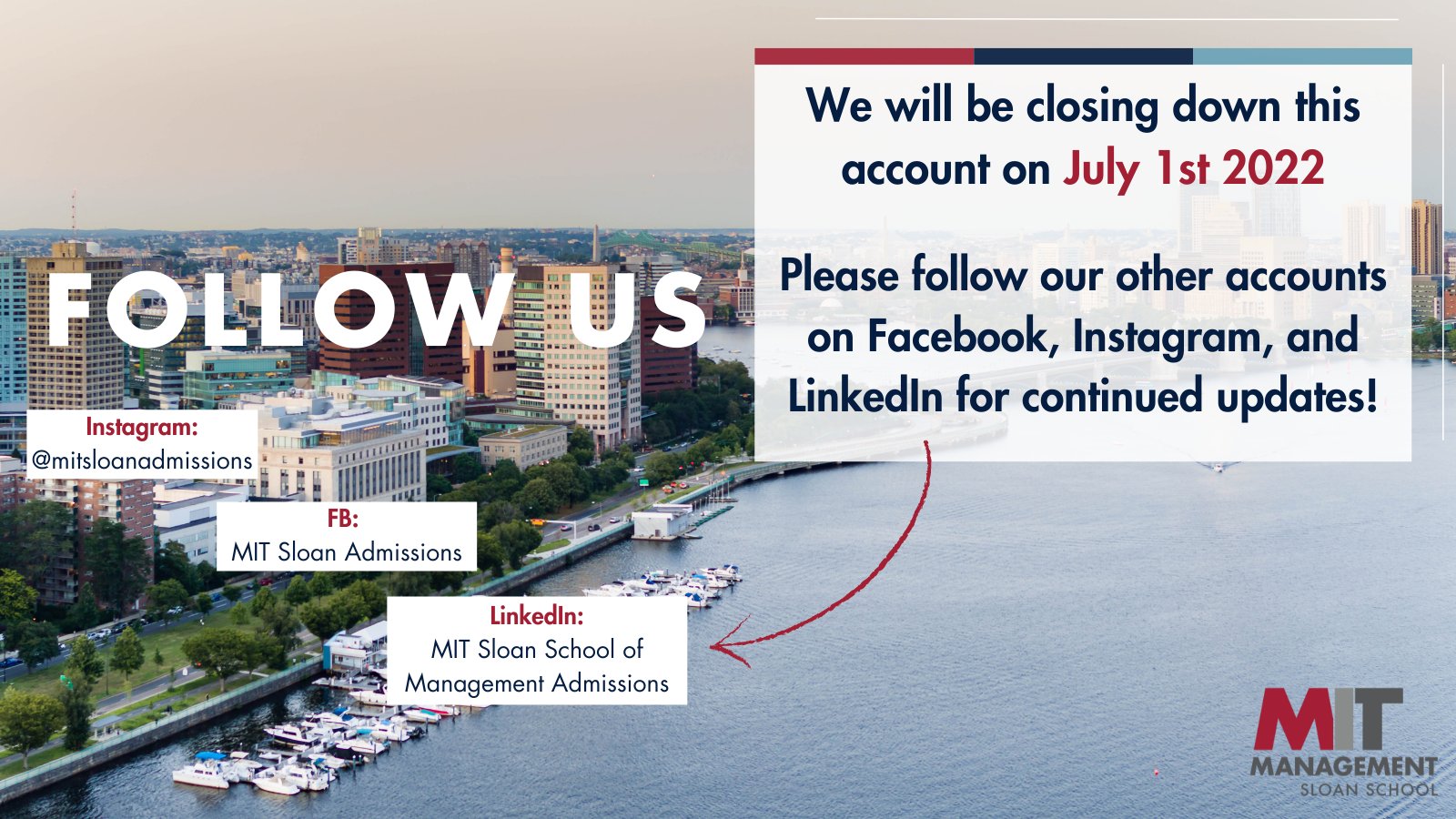
A RAID log is a valuable tool to manage your project. It can help you to identify risks and understand what your assumptions are. It can help you manage problems and improve your project.
RAID logs can be used to communicate between project managers with stakeholders. It contains detailed information about decisions and activities taken during the project. It helps project managers keep track of important information and make consistent decisions. RAID logs serve many purposes. You can keep a RAID log to monitor the progress of your project and learn from past failures so that you can improve your next one.
RAID logs are used by project managers to help them identify risks and assess their impacts before deciding on a course. These logs can either be used as a preventive measure to eliminate potential risks or as an additional tool to help you understand the possible impacts on your project. This is an important step that you should take before the project starts.
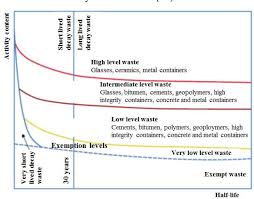
Projects cannot be avoided. They are often the hardest aspect of a project that you need to manage. Inability to take the right actions could result in poor delivery and a failure of the project. It is crucial to identify and plan for mitigation of risks early in your project.
The risk can be classified into either Low Impact items, with a low impact on a project, or High Impact items with a large negative impact. The best way of assessing the risk of an item is to measure its likelihood and severity. Both factors can be reduced to increase the chance of a risk being addressed. If either factor is increased, the risk becomes more severe. You should therefore monitor the severity and impact of any risks.
Another major component of projects are assumptions. Even though you might not be able to prove a point, it is still a good idea to record your assumptions. There are many ways you can record assumptions. However, the RAID Log is a great place to begin. Some Project/Program Managers prefer to be the sole author of their RAID log, while others prefer to use other tools as an issues log. It is important to properly document your assumptions. However, these are often better used for long term projects.
RAID logs are important tools for evaluating risk. They should be kept up-to-date throughout the project. It is also a good reference document to use as a communication tool. This is important especially for audits or status reports. This log should be updated as new issues or risks arise. It can also be used to track the progress of your team.
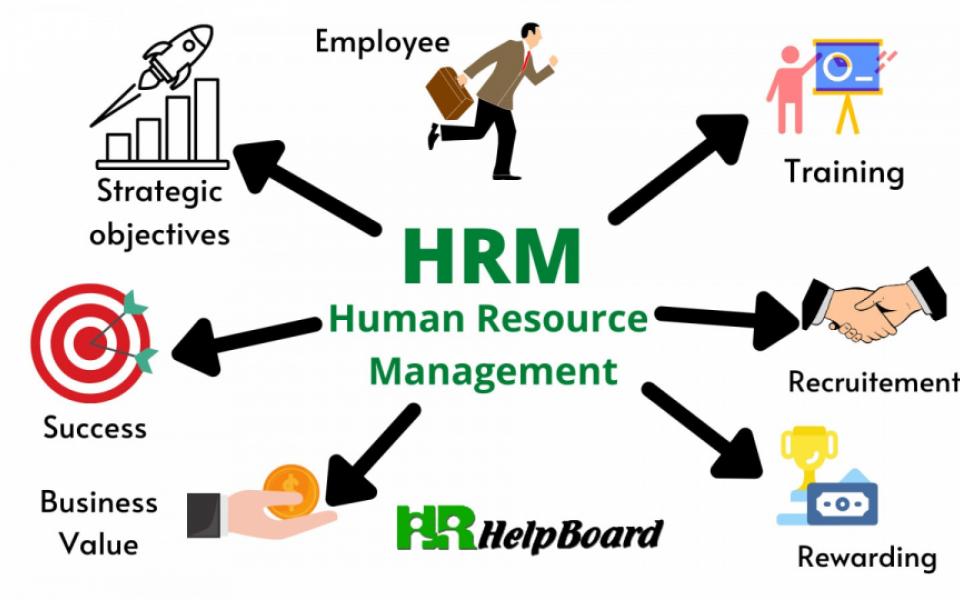
RAID logs can be very useful to project managers, particularly in the early stages. It can help you to be more organized, and keep all of the important information in one place. The RAID log can be used to track assumptions, collect data, and explain project issues to stakeholders.
FAQ
What is Six Sigma?
Six Sigma uses statistical analyses to locate problems, measure them, analyze root cause, fix problems and learn from the experience.
The first step in solving a problem is to identify it.
Next, data is collected and analyzed to identify trends and patterns.
The problem is then rectified.
Finally, data is reanalyzed to determine whether the problem has been eliminated.
This continues until you solve the problem.
What are your main management skills
No matter if they are running a local business or an international one, management skills are vital. These include the ability and willingness to manage people, finances as well resources, time and space.
These skills are necessary for setting goals and objectives as well as planning strategies, leading groups, motivating employees and solving problems.
There are so many managerial tasks!
What is Six Sigma and how can it help you?
It's a method for quality improvement that focuses on customer service as well as continuous learning. The goal is to eliminate defects by using statistical techniques.
Six Sigma was developed at Motorola in 1986 as part of its efforts to improve manufacturing processes.
This idea quickly spread throughout the industry. Today, many organizations use six sigma methods for product design, production and delivery.
What are management principles?
Management Concepts are the principles and practices managers use to manage people and resources. They cover topics like job descriptions (job descriptions), performance evaluations, training programmes, employee motivation and compensation systems.
Statistics
- As of 2020, personal bankers or tellers make an average of $32,620 per year, according to the BLS. (wgu.edu)
- Hire the top business lawyers and save up to 60% on legal fees (upcounsel.com)
- UpCounsel accepts only the top 5 percent of lawyers on its site. (upcounsel.com)
- The profession is expected to grow 7% by 2028, a bit faster than the national average. (wgu.edu)
- The average salary for financial advisors in 2021 is around $60,000 per year, with the top 10% of the profession making more than $111,000 per year. (wgu.edu)
External Links
How To
How is Lean Manufacturing done?
Lean Manufacturing processes are used to reduce waste and improve efficiency through structured methods. They were created by Toyota Motor Corporation in Japan in the 1980s. The aim was to produce better quality products at lower costs. Lean manufacturing eliminates unnecessary steps and activities from a production process. It includes five main elements: pull systems (continuous improvement), continuous improvement (just-in-time), kaizen (5S), and continuous change (continuous changes). Pull systems allow customers to get exactly what they want without having to do extra work. Continuous improvement means continuously improving on existing processes. Just-in-time refers to when components and materials are delivered directly to the point where they are needed. Kaizen stands for continuous improvement. Kaizen can be described as a process of making small improvements continuously. Last but not least, 5S is for sort. These five elements are used together to ensure the best possible results.
Lean Production System
The lean production system is based on six key concepts:
-
Flow - The focus is on moving information and material as close as possible to customers.
-
Value stream mapping - break down each stage of a process into discrete tasks and create a flowchart of the entire process;
-
Five S's - Sort, Set In Order, Shine, Standardize, and Sustain;
-
Kanban is a visual system that uses visual cues like stickers, colored tape or stickers to keep track and monitor inventory.
-
Theory of Constraints - Identify bottlenecks in the process, and eliminate them using lean tools such kanban boards.
-
Just-intime - Order components and materials at your location right on the spot.
-
Continuous improvement - Make incremental improvements rather than overhauling the entire process.