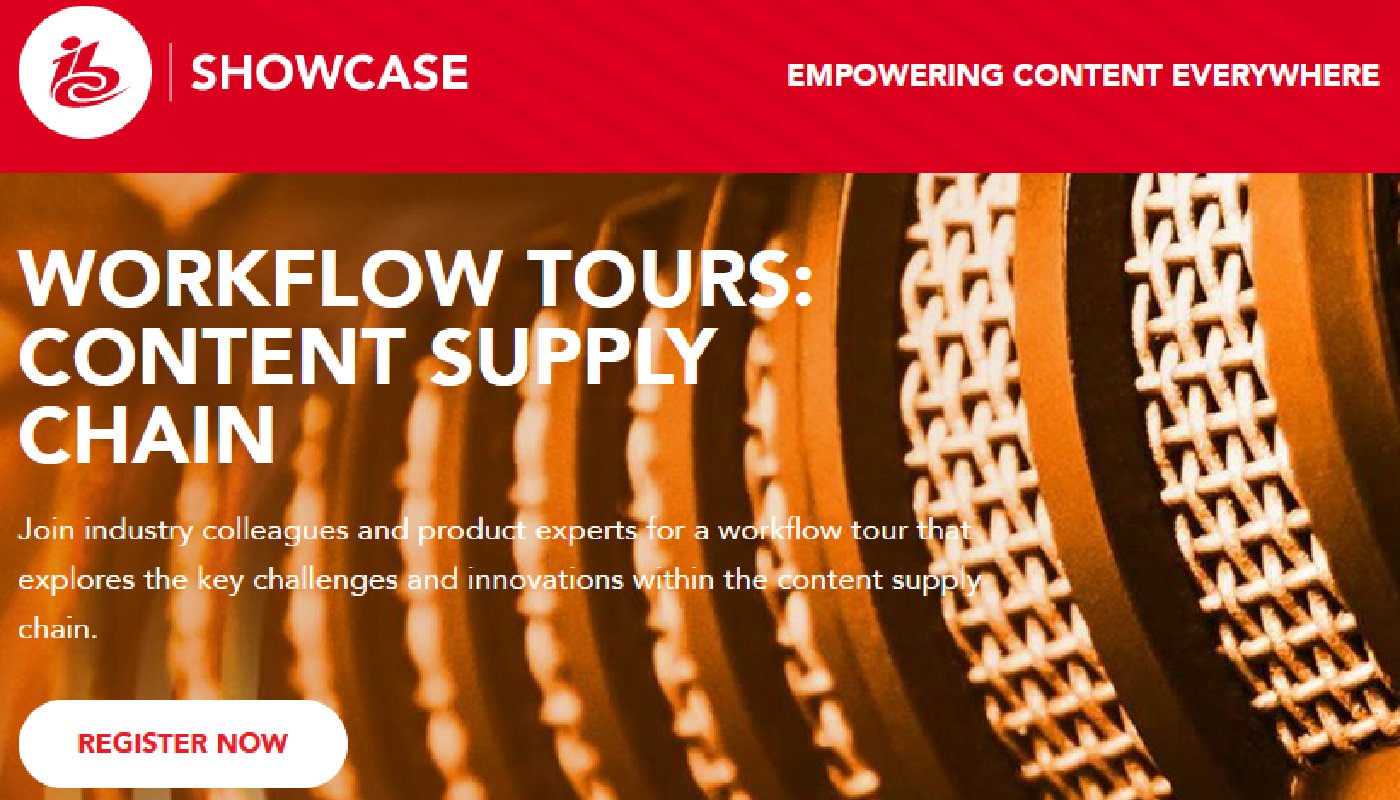
Embracing safety as a culture can be challenging, but it can be done. We'll be talking about how to establish a culture of safety in this article. This process will differ depending on what your company does. The first step is to create a safe environment. Focus groups is a common way to accomplish this. Focus groups allow you to ask employees and stakeholders for feedback. This will help to create a culture that is well-designed.
Safety as a cultural value
Safety culture is about focusing on employees and understanding that everyone has a responsibility for safety. This requires extensive education and training. This requires support at all levels. Embracing safety as a culture is an important step in improving the safety culture of an organization. But how can you achieve this? How can you create a culture that values safety? Here are some suggestions.
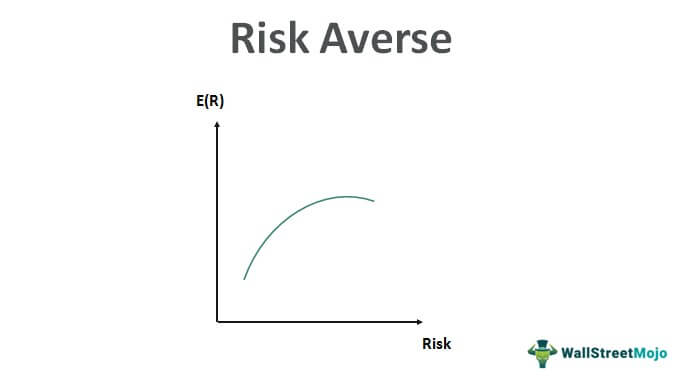
Culture shifts are the key to solving workplace safety issues. If people change the way they think about safety, it will be easier for them to take control of the whole process. Embracing safety as a culture will empower every employee to become a safety leader. Safety management systems must be able to teach employees how they can coach and lead other employees in order to create such a culture. Employees must also be committed to safety.
Safety culture for the analytical stage
A safety culture that encourages employees and their families to report safety hazards is effective. The key ingredient for this is trust. Employees should feel confident that they won't lose their job or be punished for reporting problems. Senior management must sign a non-reprisal agreement to ensure that confidential information is not shared. Furthermore, employees must feel confident that the information will be treated in a timely manner.
Analytical stage in safety culture is where problems are identified, analysed, and reported back to the reporting team. These include corrective actions programs and root-cause analyses. These tools help identify the root causes of injury-producing incidents, which is crucial for safe systems of care. This analytical stage is essential to creating a safety culture. It is important to identify the values, attitudes, and beliefs that will drive safety culture.
With focus groups, creating a safety culture
You need flexibility and a strategic plan to establish a safety culture. Employees must feel comfortable sharing concerns and ideas regarding workplace safety. A whistleblowing system allows employees to anonymously report unsafe behavior. This will help facilitate this. Instead of punishing people for pointing out problems, emphasize positive reinforcement. Positive reinforcement fosters trust and morale as well as encourages employee engagement. A safety culture can be a long-term endeavor, but it is well worth the effort.
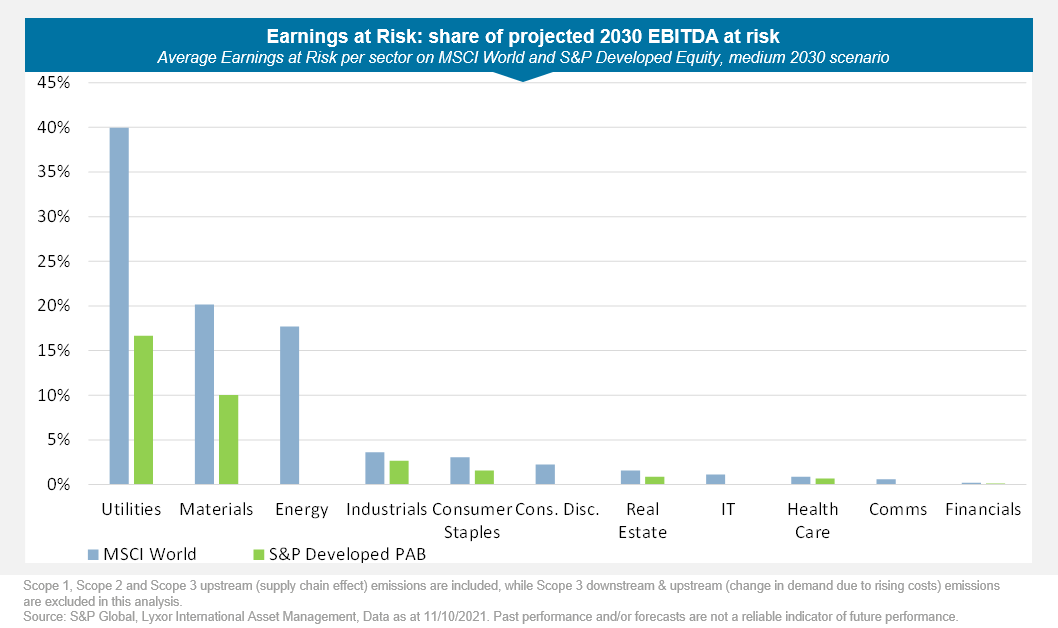
Companies need to first recognize their limiting thoughts in order to build a safe environment. Once they have identified these mindsets, they must orchestrate mind-set shifts. They must create trust and a positive atmosphere that encourages employees to report incidents and near misses. This will help employees see that reporting incidents and near misses is rewarding. This will ultimately result in more safety-conscious behavior.
FAQ
How can we create a successful company culture?
A company culture that values and respects its employees is a successful one.
It's built on three fundamental principles:
-
Everybody has something to offer.
-
Fair treatment of people is the goal
-
Respect is shared between individuals and groups
These values are evident in the way that people act. They will show consideration and courtesy to others.
They will respect other people's opinions.
They encourage others to express their feelings and ideas.
Additionally, the company culture encourages open communication as well as collaboration.
People are free to speak out without fear of reprisal.
They understand that mistakes can be forgiven as long as they're dealt with honestly.
Finally, the company culture promotes integrity and honesty.
Everyone understands that the truth is always best.
Everyone recognizes that rules and regulations are important to follow.
And no one expects special treatment or favors.
What does Six Sigma mean?
Six Sigma uses statistical analysis to find problems, measure them, analyze root causes, correct problems, and learn from experience.
The first step to solving the problem is to identify it.
The next step is to collect data and analyze it in order to identify trends or patterns.
The problem is then rectified.
Finally, data will be reanalyzed to determine if there is an issue.
This continues until the problem has been solved.
What can a manager do to improve his/her management skillset?
By practicing good management skills at all times.
Managers need to monitor their subordinates' performance.
You must act quickly if you notice that your subordinate isn’t performing to their standards.
It is important to be able identify areas that need improvement and what can be done to improve them.
What are the 4 main functions of management?
Management is responsible of planning, organizing, leading, and controlling people as well as resources. It includes creating policies and procedures, as well setting goals.
Management assists an organization in achieving its goals by providing direction, coordination and control, leadership, motivation, supervision and training, as well as evaluation.
Management's four main functions are:
Planning - Planning involves determining what needs to be done.
Organizing – Organizing means deciding how to organize things.
Directing - Directing means getting people to follow instructions.
Controlling: Controlling refers to making sure that people do what they are supposed to.
What are the steps in the decision-making process in management?
The decision-making process for managers is complex and multifaceted. It involves many factors, such as analysis and strategy, planning, execution, measurement, evaluation, feedback etc.
The key thing to remember when managing people is that they are human beings just as you are and therefore make mistakes. As such, there is always room for improvement, especially if you're willing to put forth the effort to improve yourself first.
This video shows you how management makes decisions. We will discuss the various types of decisions, and why they are so important. Every manager should be able to make them. The following topics will be covered:
Statistics
- The profession is expected to grow 7% by 2028, a bit faster than the national average. (wgu.edu)
- As of 2020, personal bankers or tellers make an average of $32,620 per year, according to the BLS. (wgu.edu)
- Hire the top business lawyers and save up to 60% on legal fees (upcounsel.com)
- The average salary for financial advisors in 2021 is around $60,000 per year, with the top 10% of the profession making more than $111,000 per year. (wgu.edu)
- Your choice in Step 5 may very likely be the same or similar to the alternative you placed at the top of your list at the end of Step 4. (umassd.edu)
External Links
How To
How can you use the Kaizen method?
Kaizen means continuous improvement. This term was first used by Toyota Motor Corporation in the 1950s. It refers to the Japanese philosophy that emphasizes continuous improvement through small incremental changes. It's a team effort to continuously improve processes.
Kaizen is one method that Lean Manufacturing uses to its greatest advantage. In this concept, employees who are responsible for the production line must identify problems that exist during the manufacturing process and try to solve them before they become big issues. This is how you can improve the quality and lower the cost.
The main idea behind kaizen is to make every worker aware of what happens around him/her. To prevent problems from happening, any problem should be addressed immediately. If someone is aware of a problem at work, he/she should inform his/her manager immediately.
Kaizen has a set of basic principles that we all follow. When working with kaizen, we always start with the end result and move towards the beginning. In order to improve our factory's production, we must first fix the machines producing the final product. Next, we fix the machines which produce components. We then fix the workers that work with those machines.
This is why it's called "kaizen" because it works step-by-step to improve everything. We finish fixing the factory and then go back to the beginning. This continues until we achieve perfection.
To implement kaizen in your business, you need to find out how to measure its effectiveness. There are many ways you can determine if kaizen has been implemented well. Another way to determine if kaizen is working well is to look at the quality of the products. Another way is to check how much productivity has grown since kaizen was implemented.
Another way to know whether kaizen is working is to ask yourself why did you decide to implement kaizen. Did you do it because it was legal or to save money? It was a way to save money or help you succeed.
Congratulations! You are ready to start kaizen.