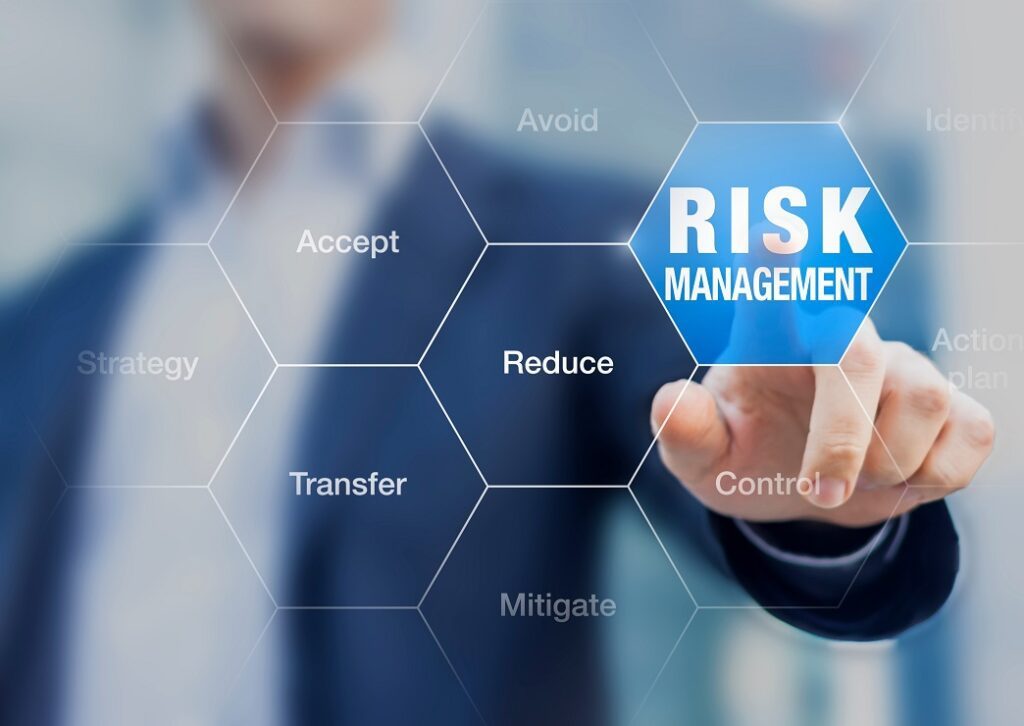
Project management involves the practice of guiding, managing and controlling all processes within a company. It assists companies in setting realistic goals, budgets, timeframes, and deadlines. It assists teams in creating a plan to achieve goals and minimize risk. Companies strive to integrate project management into the overall business strategy. This helps them maximize their resources and prevents money from being wasted.
Lean project management
Any company's goal is to offer a product or service its customers will be willing to pay for. Customer needs are what determine the product's value. The product or service provides a solution to their problem or part of the solution. Processes that don't add value to the customer are considered waste. A series of questions should be asked by Lean teams to determine what is value.
Lean teams must be able to track their progress and stay on top of it. They must evaluate both the effectiveness of their solutions and their results. They should also seek out the root cause for any problems. They can then improve and continue improving their processes.
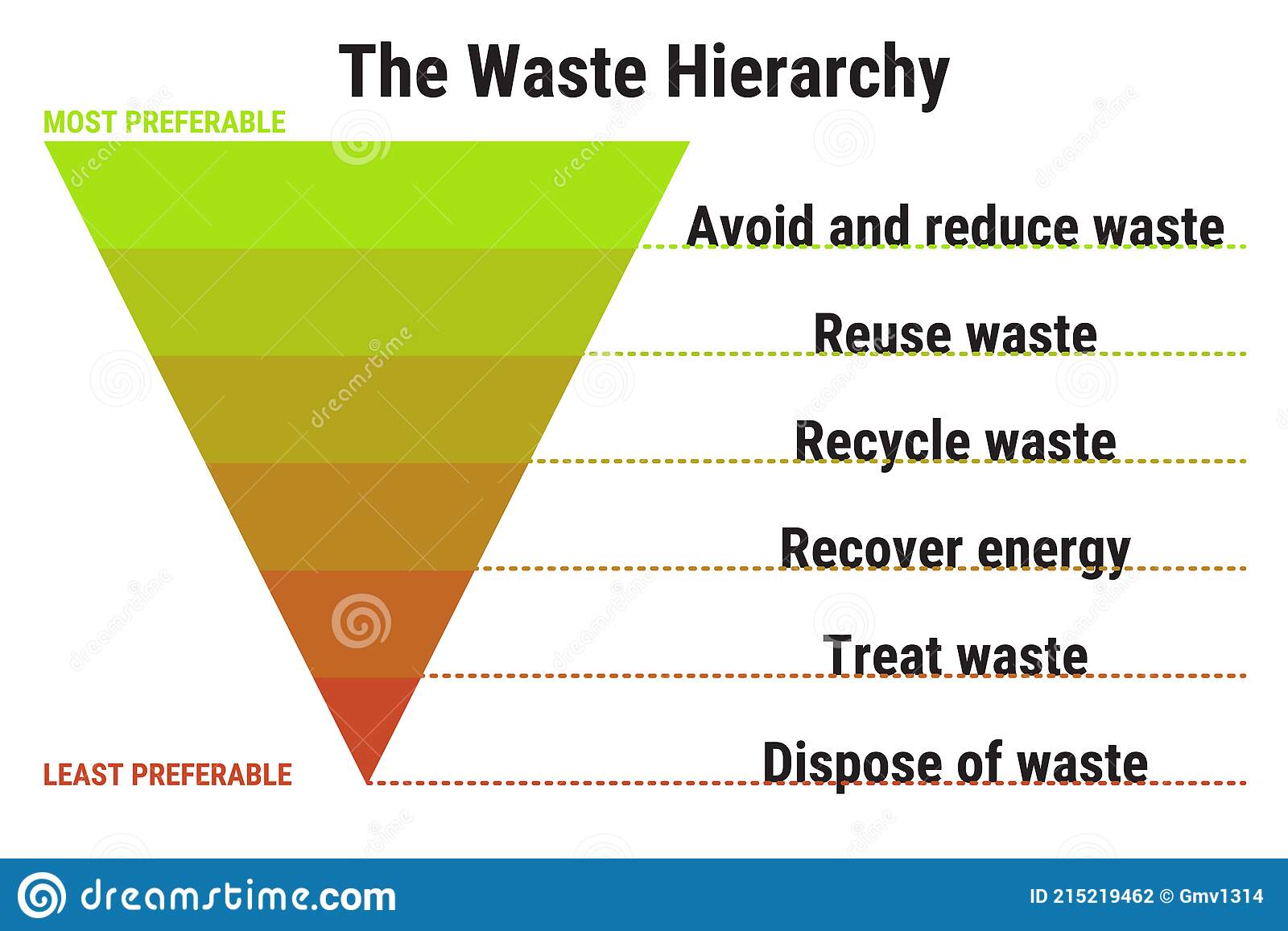
Agile project management
Introducing Agile project management into your company is an excellent way to implement new methods for developing and executing projects. This working method is based in the principle of empowering smart, self directed teams to create solutions. Customers are also invited to participate in the development process of agile teams by offering feedback. These teams are more open to trying new ideas and can improvise.
Agile and traditional project management have many differences. Agile can be agile enough to adapt quickly to change. Agile allows teams and individuals to make changes all through the project. Traditional project management tends to focus on the initial stages. Agile, however, is more flexible. There are many opportunities to make course corrections or improvements to the product or its processes.
Traditional project management
The planning phase is the most important part of traditional project management. This phase assists the manager in establishing costs, schedules, resources, and other details for the project. It is also a good way to set clear expectations so that all parties are aware of the timeline, and the expected outcome. Project managers also try to avoid any duplication or overlap.
Traditional project management offers the main benefits of consistency and predictability. Because the objectives of the project are known in advance, they can be executed efficiently and with minimal supervision. It can work within a budget and has a predictable schedule. It reduces the risk of unexpected expenses.
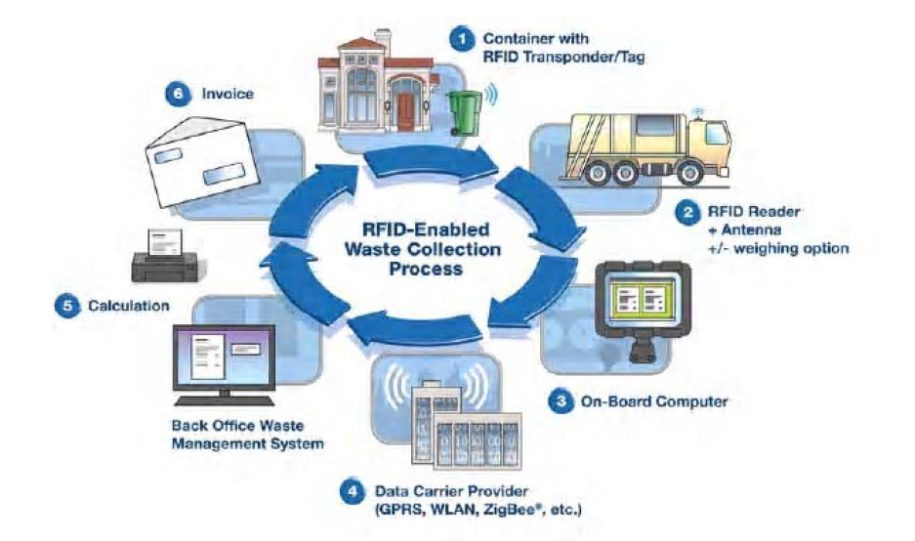
Change management
Management of change in a company is the process of implementing new processes or programs. It involves identifying and preparing people to implement the change. This includes ensuring that all aspects, both technical and business, of the project are covered.
The goal of change management involves implementing changes that will improve an organization. It will allow the organization to increase revenue, solve challenges, and create opportunities. It will also assist in improving alignment and information flow.
FAQ
What role can a manager fill in a company’s management?
Different industries have different roles for managers.
In general, a manager controls the day-to-day operations of a company.
He/she will ensure that the company fulfills its financial obligations.
He/she makes sure that employees adhere to the rules and regulations as well as quality standards.
He/she plans and oversees marketing campaigns.
What is the meaning of "project management?"
This refers to managing all activities that are involved in a project's execution.
We help you define the scope of your project, identify the requirements, prepare the budget, organize the team, plan the work, monitor progress and evaluate the results before closing down the project.
What is the difference between Six Sigma Six Sigma and TQM?
The main difference between these two quality management tools is that six sigma focuses on eliminating defects while total quality management (TQM) focuses on improving processes and reducing costs.
Six Sigma is an approach for continuous improvement. This approach emphasizes eliminating defects through statistical methods like control charts, Pareto analysis, and p-charts.
This method attempts to reduce variations in product output. This is accomplished by identifying the root cause of problems and fixing them.
Total quality management is the measurement and monitoring of all aspects within an organization. It also involves training employees to improve performance.
It is used to increase productivity.
How does a manager learn to manage?
Good management skills are essential for success.
Managers must monitor the performance of subordinates constantly.
If you notice your subordinate isn't performing up to par, you must take action quickly.
You must be able to spot what is lacking and how you can improve it.
It can sometimes seem difficult to make business decisions.
Complex systems with many moving parts are the hallmark of businesses. The people who run them must juggle multiple priorities at once while also dealing with uncertainty and complexity.
Understanding the impact of these factors on the system is crucial to making sound decisions.
It is important to consider the functions and reasons for each part of the system. It's important to also consider how they interact with each other.
Ask yourself if there are hidden assumptions that have influenced your behavior. If they don't, you may want to reconsider them.
Try asking for help from another person if you're still stuck. They might have different perspectives than you, and could offer insight that could help you solve your problem.
How does a manager motivate their employees?
Motivation is the desire to do well.
Engaging in something fun can be a great way to get motivated.
Another way to get motivated is to see yourself as a contributor to the success of the company.
For example, if you want to become a doctor, you'll probably find it more motivating to see patients than to study medicine books all day.
A different type of motivation comes directly from the inside.
You may feel strongly that you are responsible to help others.
Or you might enjoy working hard.
If you don’t feel motivated, find out why.
You can then think of ways to improve your motivation.
Statistics
- Your choice in Step 5 may very likely be the same or similar to the alternative you placed at the top of your list at the end of Step 4. (umassd.edu)
- As of 2020, personal bankers or tellers make an average of $32,620 per year, according to the BLS. (wgu.edu)
- UpCounsel accepts only the top 5 percent of lawyers on its site. (upcounsel.com)
- The profession is expected to grow 7% by 2028, a bit faster than the national average. (wgu.edu)
- The BLS says that financial services jobs like banking are expected to grow 4% by 2030, about as fast as the national average. (wgu.edu)
External Links
How To
How can you use the Kaizen method?
Kaizen means continuous improvement. This term was first used by Toyota Motor Corporation in the 1950s. It refers to the Japanese philosophy that emphasizes continuous improvement through small incremental changes. This is a collaborative process in which people work together to improve their processes continually.
Kaizen is one of Lean Manufacturing's most efficient methods. Kaizen is a concept where employees in charge of the production line are required to spot problems during the manufacturing process before they become major issues. This way, the quality of products increases, and the cost decreases.
Kaizen is about making everyone aware of the world around them. Correct any errors immediately to avoid future problems. If someone spots a problem while at work, they should immediately report it to their manager.
Kaizen follows a set of principles. The end product is always our starting point and we work toward the beginning. If we want to improve our factory for example, we start by fixing the machines that make the final product. Then, we fix the machines that produce components and then the ones that produce raw materials. Then we fix the workers, who directly work with these machines.
This method is known as kaizen because it focuses upon improving every aspect of the process step by step. We finish fixing the factory and then go back to the beginning. This continues until we achieve perfection.
Before you can implement kaizen into your business, it is necessary to learn how to measure its effectiveness. There are many ways to tell if kaizen is effective. One way is to examine the amount of defects on the final products. Another way is determining how much productivity increased after implementing kaizen.
A good way to determine whether kaizen has been implemented is to ask why. Is it because the law required it or because you want to save money. Did you really believe it would lead to success?
Congratulations! You are ready to start kaizen.