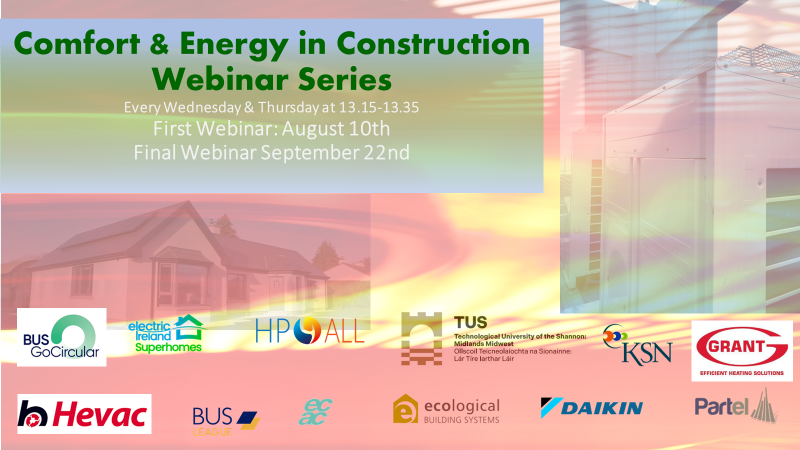
Obtaining a degree in project management can be a great way to jumpstart your career. This degree will equip you with the necessary skills to be a valuable member of any team. It also helps you become a well-rounded individual with a keen sense of problem solving and coordination skills. There are many career options that will require these skills. Some areas require them most, such a financial and healthcare industry.
Project management involves planning, organizing, executing and controlling work. It is widely used in all industries, from construction to technology. It can be used to implement a marketing strategy, or to build a project. It can also be used in a cost-benefit analysis. It is a difficult subject to understand.
You can take many courses to learn project management. You can take an introductory online course, such as those offered by edX, to learn about the subject. Project management internships are a great way to get hands-on experience. It is a good idea to talk with other project managers to determine the best course of action.
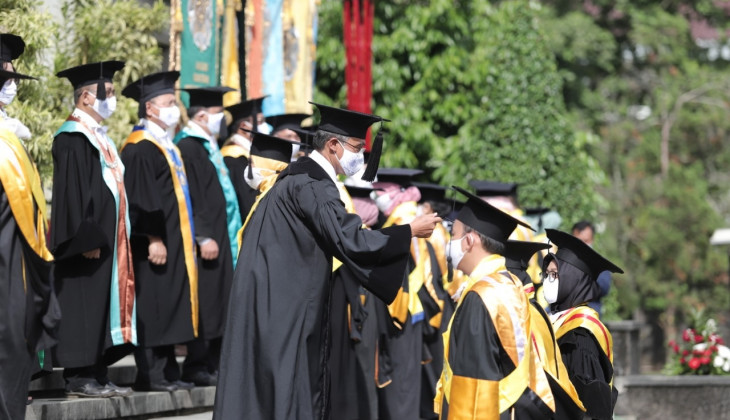
Project management is not as complex as it seems. It is more complicated than simply writing a resume. However, the skills learned can make a huge difference in your career. You might find that healthcare careers require the ability to transform ideas into reality. This skill can be learned and developed through a project management course.
Communication is an essential part of project management. Proper communication will help you eliminate bottlenecks, reduce errors, and increase your achievement. You must work together with your team to achieve project completion on time and within budget. Project management is a team sport. It's a great idea to take an introductory online course. However, you might want consult other project managers about the best course for you.
Many courses in project management include interesting and informative content. You will find that the best courses include both hands-on activities such as threaded cases and class discussions. You will also learn about the different tools and techniques used in project management. Read stories from other project managers to gain a better understanding.
Remember that you will not be able to complete a project management course in just one semester. To complete a project management degree, it will take about one year. All courses are required for your certificate. You'll also need to complete an internship in order to see if you're a good fit for the career.
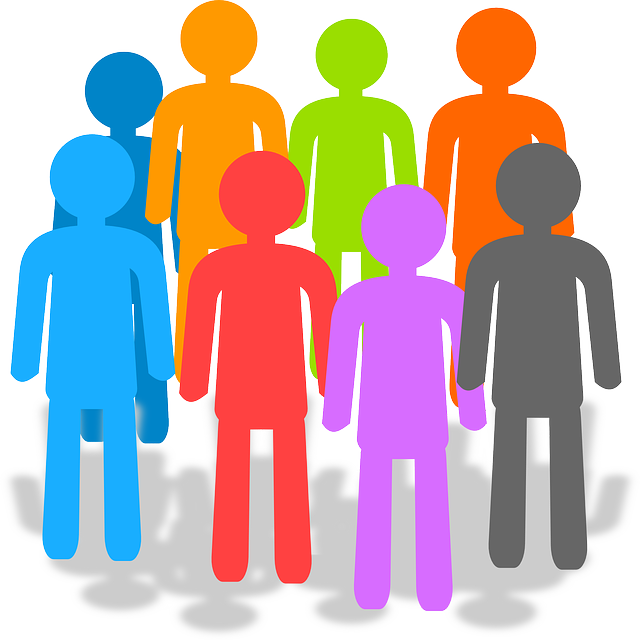
A series of workshops and coaching sessions are included in the course to assist you. You'll learn the best ways to communicate with your team and how to develop a structured methodology based on the Project Management Body of Knowledge (PMBOK). It's important to be able recognize which techniques and tools are most effective for you.
FAQ
How can a manager improve his/her managerial skills?
It is important to have good management skills.
Managers must monitor the performance of subordinates constantly.
It is important to take immediate action if your subordinate doesn't perform as expected.
It is important to be able identify areas that need improvement and what can be done to improve them.
How does Six Sigma work
Six Sigma uses statistical analysis to find problems, measure them, analyze root causes, correct problems, and learn from experience.
The first step to solving the problem is to identify it.
Next, data is collected and analyzed to identify trends and patterns.
Then corrective actions are taken to solve the problem.
Finally, data is reanalyzed to determine whether the problem has been eliminated.
This continues until you solve the problem.
How do we create a company culture that is productive?
A company culture that values and respects its employees is a successful one.
It is founded on three basic principles:
-
Everybody has something to offer.
-
People are treated fairly
-
People and groups should respect each other.
These values are reflected by the way people behave. They will show consideration and courtesy to others.
They will respect the opinions of others.
They encourage others to express their feelings and ideas.
The company culture promotes collaboration and open communication.
People feel free to express their views openly without fear of reprisal.
They are aware that mistakes can be accepted if they are treated honestly.
The company culture encourages honesty and integrity.
Everyone knows that they must always tell the truth.
Everyone recognizes that rules and regulations are important to follow.
And no one expects special treatment or favors.
Statistics
- The profession is expected to grow 7% by 2028, a bit faster than the national average. (wgu.edu)
- Our program is 100% engineered for your success. (online.uc.edu)
- Your choice in Step 5 may very likely be the same or similar to the alternative you placed at the top of your list at the end of Step 4. (umassd.edu)
- As of 2020, personal bankers or tellers make an average of $32,620 per year, according to the BLS. (wgu.edu)
- The BLS says that financial services jobs like banking are expected to grow 4% by 2030, about as fast as the national average. (wgu.edu)
External Links
How To
How is Lean Manufacturing done?
Lean Manufacturing techniques are used to reduce waste while increasing efficiency by using structured methods. They were developed in Japan by Toyota Motor Corporation (in the 1980s). The goal was to produce quality products at lower cost. Lean manufacturing emphasizes removing unnecessary steps from the production process. It is made up of five elements: continuous improvement, continuous improvement, just in-time, continuous change, and 5S. The production of only what the customer needs without extra work is called pull systems. Continuous improvement is the continuous improvement of existing processes. Just-intime refers the time components and materials arrive at the exact place where they are needed. Kaizen is continuous improvement. This can be achieved by making small, incremental changes every day. Last but not least, 5S is for sort. These five elements can be combined to achieve the best possible results.
The Lean Production System
Six key concepts make up the lean manufacturing system.
-
Flow - The focus is on moving information and material as close as possible to customers.
-
Value stream mapping: This is a way to break down each stage into separate tasks and create a flowchart for the entire process.
-
Five S's, Sort, Set in Order, Shine. Standardize. and Sustain.
-
Kanban is a visual system that uses visual cues like stickers, colored tape or stickers to keep track and monitor inventory.
-
Theory of constraints - identify bottlenecks during the process and eliminate them with lean tools like Kanban boards.
-
Just-in time - Get components and materials delivered right at the point of usage;
-
Continuous improvement: Make incremental improvements to the process instead of overhauling it completely.