
Online engineering management degrees are available. A BSc in engineering management can be obtained online. You will need to complete ME, EE and CS classes. Capstone classes run two semesters in a row. You will also have to take a capstone project. If you want to get your degree online, you need to meet certain requirements. To determine if this program is right for your needs, you need to find out the requirements.
BS in engineering management
Asu offers a Bachelor of Science in Engineering Management, which gives students advanced knowledge in engineering management. It also helps them develop leadership skills. The program combines core business courses and coursework in engineering and administration. These include organizational behavior, finance, managerial accounting, and financial management. The program prepares students for a variety management positions including those in quality control systems and industrial production. The flexibility and affordability of the program, as well as its easy online learning options, have made it a very popular option for engineering students.
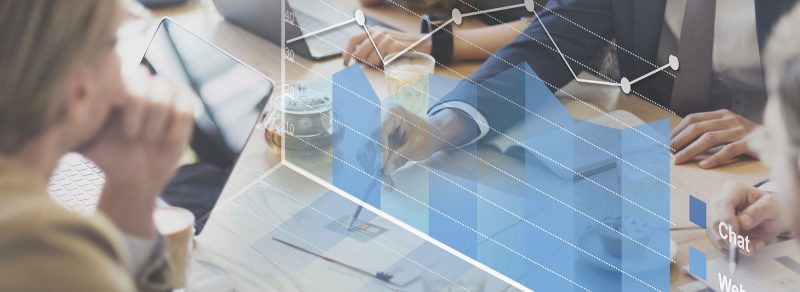
The BS in engineering management degree emphasizes analytical and management principles, while still emphasizing technical engineering expertise. Students will learn to blend the two and apply them to organizational goals. The program is flexible, and students can pursue their degree online while still working in their current position. Students can explore other career options because of the program's flexibility. This program is perfect for anyone who wants to combine passion for management and technology.
Online programs in engineering management
Online engineering management programs are a great way to get the education that you want, whether you're looking for a job in tech or advancing your career. These online degrees give you the skills to lead the day-today operations of an engineering business. While you might not have an engineering degree, you can still pursue a career in this field by earning a master's in civil engineering with a specialization in engineering management.
A Master's degree in Engineering Management can be obtained online at the University of Maryland's A. James Clark School of Engineering. This program of thirty credits prepares engineers to hold executive-level jobs. It integrates management principles and sound engineering principles. It is the first college level engineering management program to be accredited by the Project Management Institute Global Accreditation Center. Drexel University’s online Master of Engineering Management program can be adapted to your schedule and only requires one or two classes per quarter. Your program can be completed in as little as two years depending on your schedule.
Entry requirements for management programs in engineering
To be eligible to apply for an engineering management program, you must meet the following minimum criteria. You must have a bachelor's degree in a technical field, with relevant courses in computer programming and statistics. You should also have a grade point average of 3.0 or higher in the last two years of undergraduate study. In addition, you must complete nine credits of electives, such as Problems in Engineering Management.
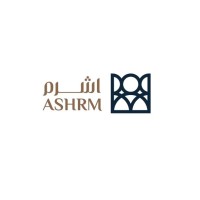
To be admitted, you will need to have an undergraduate degree in a science-related area such as economics, engineering, or accounting. It is necessary to be familiar with financial and business concepts and have previous work experience. Depending on your school's requirements, you might be required to take basic economic theories in order to understand how engineering can apply them. Depending on the school you apply to, you may also have to take a prerequisite course or two. You should apply for at least four to eight programs before you choose one.
FAQ
What are management principles?
Management concepts are the principles and practices used by managers to manage people, resources. These include topics such as human resource policies and job descriptions, performance assessments, training programs and employee motivation.
What is the role of a manager in a company?
Each industry has a different role for a manager.
A manager generally manages the day to-day operations in a company.
He/she makes sure that the company meets its financial obligations, and that it produces goods or services that customers desire.
He/she is responsible for ensuring that employees comply with all regulations and follow quality standards.
He/she designs new products or services and manages marketing campaigns.
How do you manage employees effectively?
Achieving employee happiness and productivity is key to managing them effectively.
It is important to set clear expectations about their behavior and keep track of their performance.
To do this successfully, managers need to set clear goals for themselves and for their teams.
They should communicate clearly with employees. They need to communicate clearly with their staff.
They should also keep records of all activities within their team. These include:
-
What did you accomplish?
-
How much work was done?
-
Who did it?
-
What was the moment it was completed?
-
Why?
This information is useful for monitoring performance and evaluating the results.
What is Six Sigma, exactly?
It's a method for quality improvement that focuses on customer service as well as continuous learning. This is an approach to quality improvement that uses statistical techniques to eliminate defects.
Motorola invented Six Sigma in 1986 as part its efforts to improve manufacturing.
The idea spread quickly throughout the industry, and today, many organizations are using six sigma methods to improve product design, production, delivery, and customer service.
How do we build a culture that is successful in our company?
A successful company culture is one that makes people feel valued and respected.
It is founded on three basic principles:
-
Everybody has something of value to share
-
People are treated fairly
-
It is possible to have mutual respect between groups and individuals
These values are evident in the way that people act. They will show consideration and courtesy to others.
They will respect the opinions of others.
These people will inspire others to share thoughts and feelings.
Additionally, the company culture encourages open communication as well as collaboration.
People are free to speak out without fear of reprisal.
They understand that errors will be tolerated as long they are corrected honestly.
Finally, the company culture promotes honesty and integrity.
Everyone knows that they must always tell truth.
Everyone knows that there are rules and regulations that apply to them.
People don't expect special treatment or favors.
Statistics
- Our program is 100% engineered for your success. (online.uc.edu)
- This field is expected to grow about 7% by 2028, a bit faster than the national average for job growth. (wgu.edu)
- Hire the top business lawyers and save up to 60% on legal fees (upcounsel.com)
- The profession is expected to grow 7% by 2028, a bit faster than the national average. (wgu.edu)
- As of 2020, personal bankers or tellers make an average of $32,620 per year, according to the BLS. (wgu.edu)
External Links
How To
How can Lean Manufacturing be done?
Lean Manufacturing methods are used to reduce waste through structured processes. They were developed in Japan by Toyota Motor Corporation (in the 1980s). The primary goal was to make products with lower costs and maintain high quality. Lean manufacturing eliminates unnecessary steps and activities from a production process. It is made up of five elements: continuous improvement, continuous improvement, just in-time, continuous change, and 5S. The production of only what the customer needs without extra work is called pull systems. Continuous improvement is constantly improving upon existing processes. Just-in-time refers to when components and materials are delivered directly to the point where they are needed. Kaizen is continuous improvement. This can be achieved by making small, incremental changes every day. Last but not least, 5S is for sort. These five elements are used together to ensure the best possible results.
The Lean Production System
The lean production system is based on six key concepts:
-
Flow - focuses on moving information and materials as close to customers as possible.
-
Value stream mapping- This allows you to break down each step of a process and create a flowchart detailing the entire process.
-
Five S's: Sort, Shine Standardize, Sustain, Set In Order, Shine and Shine
-
Kanban - use visual signals such as colored tape, stickers, or other visual cues to keep track of inventory;
-
Theory of constraints: Identify bottlenecks and use lean tools such as kanban boards to eliminate them.
-
Just-in Time - Send components and material directly to the point-of-use;
-
Continuous improvement - incremental improvements are made to the process, not a complete overhaul.