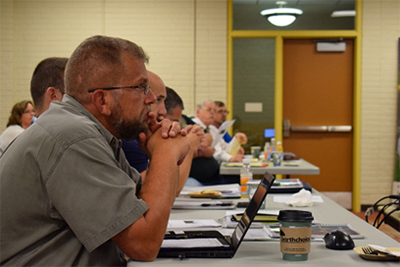
A webinar on supply chain can be a great way for you to find out more about current trends in your industry and how they affect your business. Many of these webinars are free and open for the public. Learn more about Supply Chain Management and Machine Learning. You can also learn more about Industry 4.0 technologies and Multiparty Control Towers. These events are great opportunities to get the latest information on supply chain technology, whether you are a business leader or looking for new ideas for your company.
Machine Learning
Machine Learning can be used in many ways throughout your supply chain. It can help optimize factory schedules, balance make-to-order/made-to-stock workflows, prevent material delays in production, and more. In addition, machine learning can be used to detect fraud. It analyses real-time data, looking for patterns and anomalies. Supply chain managers are notified of any problems.
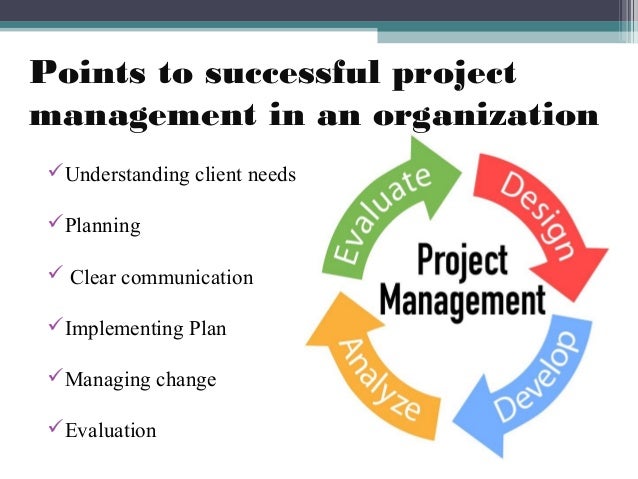
AI
Predictive Analytics is a great tool to improve supply chain efficiency. But, it can be challenging to interpret the data generated from this technology. This webinar will help supply channel managers understand AI basics and how to use it in their business.
Industry 4.0 technology
The Digital Supply Chain, or Industry 4.0, represents a fundamental shift in how businesses conduct business. It's difficult to discern the competitive advantage of new technologies because of the rapid pace at which they are changing. Fortunately, this Capstone Webinar will explain the key domains and change agents driving the transformation. You will also find answers to some of your most pressing questions about key technologies.
Multiparty control towers
Multiparty control rooms are an important component of the supply chain and offer many benefits for companies. They enable companies to automate repetitive tasks and save money and time. When used with orchestration platforms, multiparty control towers can prove to be an effective tool. These solutions can link all parts of the supply chain ecosystem. They provide a single source to truth for all those involved.
Collaboration in the supply chain
Collaboration within the supply chains is becoming a more popular strategy that can have significant benefits for a company's bottom lines. In addition to increasing operational efficiencies, collaborative relationships can also foster greater innovation and risk management. Collaboration can occur in both vertical and horizontal dimensions. However, there are key factors to be aware of.
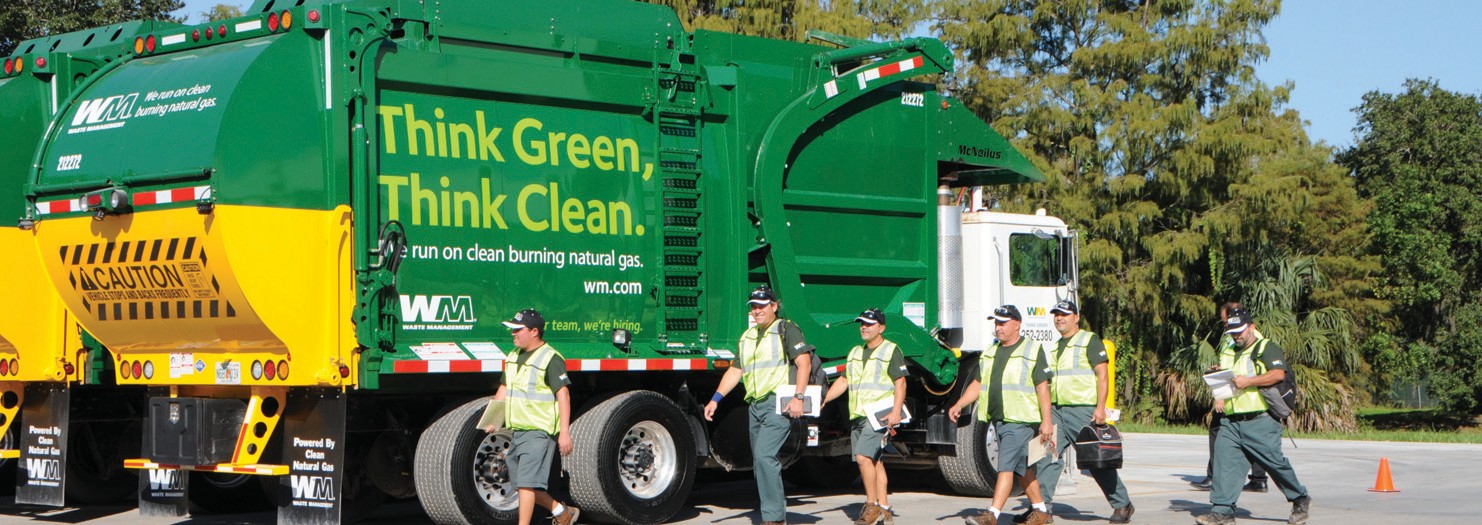
The future of supply chains
Future of the supply-chain webinars will address the problems that are affecting supply chains. They explore how to make them sustainable, integrate corporate governance into value chains, and improve the availability of medicines and medical devices for consumers. The speakers will also discuss how they can deal with increasing antitrust and ESG issues. The session will focus on trends in supply chains starting in 2022, and continuing into the future.
FAQ
Which kind of people use Six Sigma
People who have worked with statistics and operations research will usually be familiar with the concepts behind six sigma. Anyone involved in business can benefit.
It requires high levels of commitment and leadership skills to be successful.
How to effectively manage employees
Effectively managing employees means making sure they are productive and happy.
It is important to set clear expectations about their behavior and keep track of their performance.
Managers must be clear about their goals and those of their teams in order to succeed.
They need to communicate clearly and openly with staff members. They need to communicate clearly with their staff.
They must also keep track of the activities of their team. These include:
-
What did we accomplish?
-
How much work were you able to accomplish?
-
Who did it, anyway?
-
What was the moment it was completed?
-
Why was this done?
This information can be used for monitoring performance and evaluating results.
What is the meaning of "project management?"
It refers to the management of activities related to a project.
This includes defining the scope, identifying the requirements and preparing the budget. We also organize the project team, schedule the work, monitor progress, evaluate results, and close the project.
How can we create a culture of success in our company?
A positive company culture creates a sense of belonging and respect in its people.
It's built on three fundamental principles:
-
Everybody has something to offer.
-
People are treated with respect
-
People and groups should respect each other.
These values reflect in how people behave. For example, they will treat others with courtesy and consideration.
They will listen respectfully to the opinions of others.
They encourage others to express their feelings and ideas.
In addition, the company culture encourages open communication and collaboration.
People can freely express their opinions without fear or reprisal.
They understand that mistakes can be forgiven as long as they're dealt with honestly.
Finally, the company culture promotes honesty and integrity.
Everyone is aware that truth must be told.
Everyone recognizes that rules and regulations are important to follow.
No one is entitled to any special treatment or favors.
What are the five management steps?
These five stages are: planning, execution monitoring, review and evaluation.
Planning means setting goals for the long-term. Planning involves defining your goals and how to get there.
Execution is when you actually execute the plans. They must be followed by all parties.
Monitoring is the act of monitoring your progress towards achieving your targets. This should involve regular reviews of performance against targets and budgets.
Each year, reviews are held at the end. They provide an opportunity to assess whether everything went well during the year. If not, changes may be made to improve the performance next time around.
After the annual review is complete, evaluations are conducted. It helps you identify the successes and failures. It also provides feedback on how well people performed.
Statistics
- Our program is 100% engineered for your success. (online.uc.edu)
- Hire the top business lawyers and save up to 60% on legal fees (upcounsel.com)
- Your choice in Step 5 may very likely be the same or similar to the alternative you placed at the top of your list at the end of Step 4. (umassd.edu)
- 100% of the courses are offered online, and no campus visits are required — a big time-saver for you. (online.uc.edu)
- UpCounsel accepts only the top 5 percent of lawyers on its site. (upcounsel.com)
External Links
How To
How do you apply the Kaizen method to your life?
Kaizen means continuous improvement. This term was first used by Toyota Motor Corporation in the 1950s. It refers to the Japanese philosophy that emphasizes continuous improvement through small incremental changes. This is a collaborative process in which people work together to improve their processes continually.
Kaizen, a Lean Manufacturing method, is one of its most powerful. Kaizen is a concept where employees in charge of the production line are required to spot problems during the manufacturing process before they become major issues. This is how you can improve the quality and lower the cost.
Kaizen is a way to raise awareness about what's happening around you. Correct any errors immediately to avoid future problems. If someone is aware of a problem at work, he/she should inform his/her manager immediately.
Kaizen has a set of basic principles that we all follow. Always start with the end product in mind and work our way back to the beginning. To improve our factory, for example, we need to fix the machines that produce the final product. Next, we repair the machines that make components. Then, the machines that make raw materials. Then we fix the workers, who directly work with these machines.
This approach is called 'kaizen' because it focuses on improving everything steps by step. Once the factory is fixed, we return to the original site and work our way back until we get there.
To implement kaizen in your business, you need to find out how to measure its effectiveness. There are many methods to assess if kaizen works well. Another way to determine if kaizen is working well is to look at the quality of the products. Another way is to check how much productivity has grown since kaizen was implemented.
You can also find out if kaizen works by asking yourself why you decided to implement it. It was because of the law, or simply because you wanted to save some money. Did you really believe that it would be a success factor?
If you answered yes to any one of these questions, congratulations! Now you're ready for kaizen.