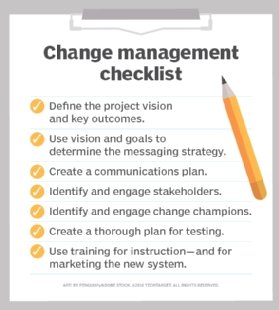
This method works best for projects that have a strict schedule and are relatively simple. The project team should coordinate early in order to resolve site-related concerns and reach project goals. Additionally, owners must clearly communicate with the architect or contractor. They must also trust each other and be clear about what they expect. If an owner is unsure, he can consult a project manager to explain the process.
IPD
IPD helps create trust and collaboration within the team to accomplish shared goals. It helps define project goals and risks for all project participants, promoting the ownership of the project and equality of the playing field among team members. It also helps reduce rework by keeping all project participants informed about progress.
The owner of the project creates an IPD group that includes key project participants. Teamwork is encouraged by the fact that incentives are tied to project milestones and goals. Participants are also compensated based on their performance. This aligns the participants' financial interests, making it predictable and manageable.
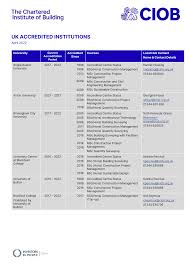
Design-Build
For many construction projects, the Design-Build project delivery option is a great choice. This method allows the owner to participate in the planning and design phases. This early collaboration helps to eliminate potential conflicts between the owner and the contractor and results in lower construction costs and a faster project schedule. Additionally, a design-build contractor eliminates the need for an in-house project manager, which allows the owner to focus on the design aspects of the project.
Contract documents should clearly define the scope of work for a Design-Build project. It is essential that the contract documents provide a clear description of the scope of work and the compensation for the design-builder during the initial stages. The contract should also outline the frequency of design submittals and the processes for review of these submissions.
Construction manager at risk
The construction manager at risk (CM at risk) method is different from traditional project delivery methods in that design and construction are separate contracts. This method selects the construction manager based not only on the lowest total cost of construction. The CM at-risk is responsible for delivering the project within the agreed price. The construction manager is also a consultant for the project owner during the design phase and as the general contractor during construction.
One of the primary advantages of this approach is the reduction of risk for all parties. This approach is not right for every project. The construction manager at risk, unlike Design-Build and Bid -Build is not an architect nor contractor. The construction manager is able to see all parties involved in the project. To avoid delay in payments, the project manger must ensure that the guaranteed maximum price is not exceeded.
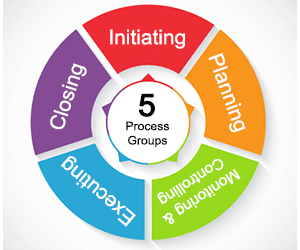
Integrated project delivery
Integrated project delivery is a way to involve all stakeholders from design through management. This approach allows all stakeholders to view the project holistically, which is a benefit to everyone. It also eliminates any waiting periods between construction phases which can lead to increased productivity. Moreover, by involving key participants early in the project, the knowledge of each team member can help improve decision-making. In addition, this method utilizes the latest technological opportunities.
Companies can solve the challenges faced during construction with an integrated project management method. To help identify the problem and take action, the Deming Cycle template can also be used by construction teams if they are unable to finish projects on time. In addition, the IPD process can facilitate a collaborative work environment and allow stakeholders to work toward a common goal.
FAQ
How do you define Six Sigma?
Six-sigma will be well-known to anyone who has worked in operations research or statistics. Anyone involved in business can benefit.
It requires high levels of commitment and leadership skills to be successful.
Why is project management so important?
To ensure projects run smoothly and meet deadlines, project management techniques are employed.
This is because most businesses rely on project work for their products and services.
These projects must be managed efficiently and effectively by companies.
Companies that do not manage their projects effectively risk losing time, money, or reputation.
What is the difference between a project and a program?
A program is permanent while a project can be temporary.
A project is usually defined by a clear goal and a set deadline.
It is often performed by a team of people, who report back on someone else.
A program typically has a set goal and objective.
It is typically done by one person.
Statistics
- The BLS says that financial services jobs like banking are expected to grow 4% by 2030, about as fast as the national average. (wgu.edu)
- UpCounsel accepts only the top 5 percent of lawyers on its site. (upcounsel.com)
- This field is expected to grow about 7% by 2028, a bit faster than the national average for job growth. (wgu.edu)
- Your choice in Step 5 may very likely be the same or similar to the alternative you placed at the top of your list at the end of Step 4. (umassd.edu)
- Hire the top business lawyers and save up to 60% on legal fees (upcounsel.com)
External Links
How To
How can you implement the Kaizen technique?
Kaizen means continuous improvement. Kaizen is a Japanese concept that encourages constant improvement by small incremental changes. It is a process where people come together to improve their processes.
Kaizen is one method that Lean Manufacturing uses to its greatest advantage. This concept requires employees to identify and solve problems during manufacturing before they become major issues. This improves the quality of products, while reducing the cost.
Kaizen is a way to raise awareness about what's happening around you. It is important to correct any problems immediately if they are discovered. It is important that employees report any problems they see while on the job to their managers.
Kaizen follows a set of principles. We always start from the end product and move toward the beginning. We can improve the factory by first fixing the machines that make it. Then, we fix the machines that produce components and then the ones that produce raw materials. And finally, we fix the workers who work directly with those machines.
This method is known as kaizen because it focuses upon improving every aspect of the process step by step. When we are done fixing the whole factory, we go back to the beginning and continue until we reach perfection.
Before you can implement kaizen into your business, it is necessary to learn how to measure its effectiveness. There are many methods to assess if kaizen works well. One way is to examine the amount of defects on the final products. Another method is to determine how much productivity has improved since the implementation of kaizen.
If you want to find out if your kaizen is actually working, ask yourself why. It was because of the law, or simply because you wanted to save some money. Did you really believe that it would be a success factor?
Suppose you answered yes to any of these questions, congratulations! You're now ready to get started with kaizen.