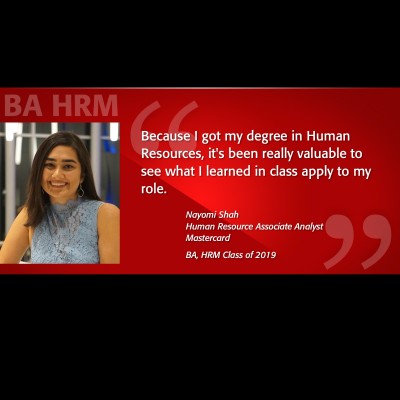
Proper waste management must always be taken into consideration when managing chemical waste or manufactured waste. To avoid the formation of harmful fumes and aerosols, incompatible substances should be stored separately in secondary containment bins. Also, incompatible chemicals shouldn't be mixed with any other chemicals. This could cause explosions or fires.
Hazards
To prevent environmental and health hazards, chemicals must be properly disposed. Proper disposal involves identifying the types of chemical waste streams that should be disposed of. This is often done at the end or an experiment. Sometimes, hazardous wastes can be mixed with regular waste to save money. However, this is not an option.
You should always check the MSDS (material safety data sheets) for hazardous chemicals before you store them. These MSDS can often be found online or at the manufacturer. These documents contain information on the chemical's hazards, such as its composition and quantity. They also contain emergency procedures such as how to deal with a spillage.
Regulations
Chemical waste management rules regulate the disposal of chemical materials in all workplaces. While most chemical wastes are created in laboratories, there are some other types that are not related to the laboratory. These include soils, building materials and lubricants. Expired chemicals must also be disposed of according to regulations.
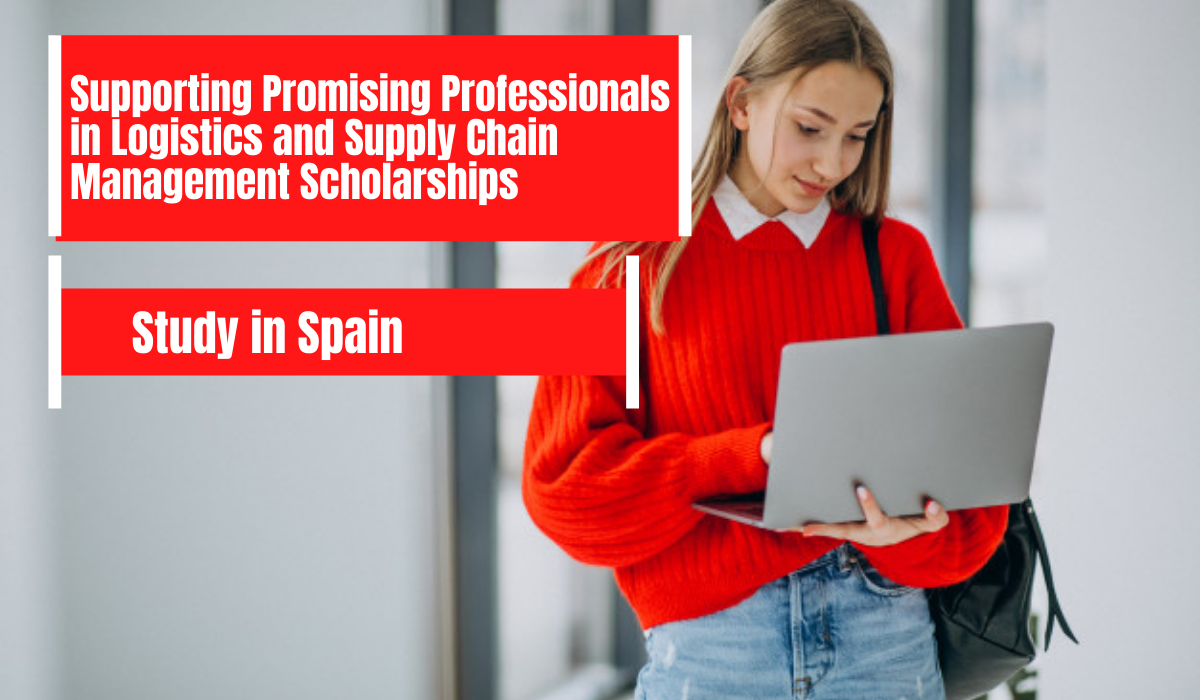
Employees are responsible for properly handling hazardous wastes. This is done to limit personal exposure and reduce the potential for environmental contamination. To assist employees in complying with regulations, two University programs have been developed to help them meet these standards.
Collection
Fill out the Chemical Collection Request form to begin the collection process. This form must also be completed for each waste container. Sometimes multiple containers of the exact same chemical waste are combined to make one request. This form is then submitted online. Upon submitting the request online, you will receive a CCR number and a Dangerous Waste label for your waste container. Once you have this information, you can print it and attach it to the waste container's label.
Chemical wastes can include any substance that is no longer useful, or a mixture of chemicals. These materials can be either in solid, liquid, and gaseous forms. To avoid pollution charges, it is crucial to collect chemical waste.
Storage
It is important to maintain proper chemical waste storage practices to avoid contamination. This is why it is important to seperate wastes according to hazard. They should be stored together in containers that are compatible. For example, chemicals containing hydrofluoric should not stored in metal or glass containers. Containers for liquid waste should be used. Small containers should not be used to store large quantities of liquids.
Containers should also be sealed tightly. Leak-proof seals are essential. Containers that contain contaminated glassware should be puncture-proof. Also, the containers should be marked hazardous waste.
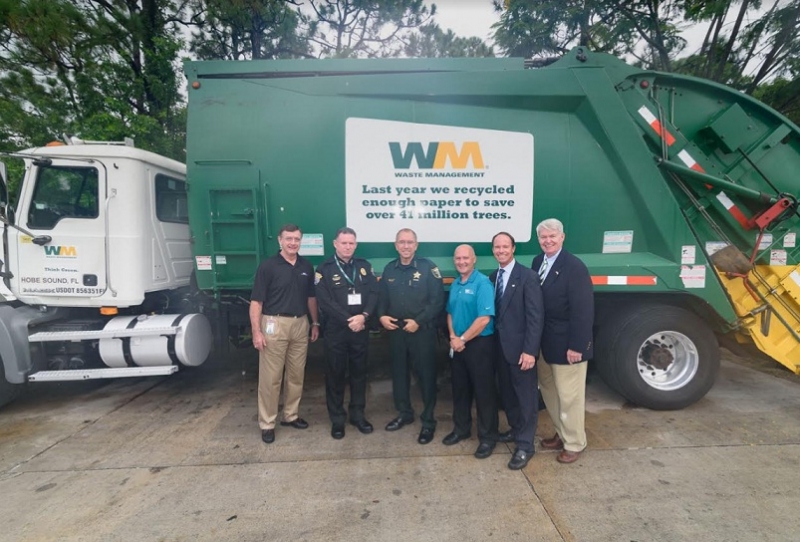
Disposal
Knowing the correct disposal procedure is essential if your company produces hazardous materials. The Texas Commission on Environmental Quality (TEQA) regulates hazardous wastes. Incorrect disposal can lead to substantial fines or legal action. A hazardous waste management system is the best way to dispose this type of waste.
Chemical waste is chemical waste that has no other use. These materials come in many forms. Some of these wastes are hazardous while others are safe. Chemical waste may be either universal or household hazardous. You must meet four requirements to be classified as hazardous. They may be flammable, radioactive, toxic, or biohazardous. For safe disposal, some chemicals should be kept in containers.
FAQ
What is the difference between a project and a program?
A project is temporary while a programme is permanent.
A project is usually defined by a clear goal and a set deadline.
It is often done in a team that reports to another.
A program often has a set goals and objectives.
It is usually done by one person.
What are the main management skills?
Managerial skills are crucial for every business owner, regardless of whether they run a small store in their locality or a large corporation. They include the ability to manage people, finances, resources, time, and space, as well as other factors.
Managerial skills are required when setting goals and objectives and planning strategies, leading employees, motivating them, solving problems, creating policies, procedures, or managing change.
As you can see there is no end to the number of managerial tasks.
What are management concepts?
Management concepts are the fundamental principles and practices that managers use when managing people and their resources. These include topics such as human resource policies and job descriptions, performance assessments, training programs and employee motivation.
Statistics
- UpCounsel accepts only the top 5 percent of lawyers on its site. (upcounsel.com)
- The average salary for financial advisors in 2021 is around $60,000 per year, with the top 10% of the profession making more than $111,000 per year. (wgu.edu)
- This field is expected to grow about 7% by 2028, a bit faster than the national average for job growth. (wgu.edu)
- Your choice in Step 5 may very likely be the same or similar to the alternative you placed at the top of your list at the end of Step 4. (umassd.edu)
- As of 2020, personal bankers or tellers make an average of $32,620 per year, according to the BLS. (wgu.edu)
External Links
How To
How is Lean Manufacturing done?
Lean Manufacturing is a method to reduce waste and increase efficiency using structured methods. They were developed in Japan by Toyota Motor Corporation (in the 1980s). The goal was to produce quality products at lower cost. Lean manufacturing eliminates unnecessary steps and activities from a production process. It is composed of five fundamental elements: continuous improvement; pull systems, continuous improvements, just-in–time, kaizen, continuous change, and 5S. The production of only what the customer needs without extra work is called pull systems. Continuous improvement is the continuous improvement of existing processes. Just-in–time refers when components or materials are delivered immediately to their intended destination. Kaizen means continuous improvement. Kaizen involves making small changes and improving continuously. Fifth, the 5S stand for sort, set up in order to shine, standardize, maintain, and standardize. These five elements work together to produce the best results.
Lean Production System
Six key concepts are the basis of lean production:
-
Flow: The goal is to move material and information as close as possible from customers.
-
Value stream mapping - Break down each stage in a process into distinct tasks and create an overview of the whole process.
-
Five S's - Sort, Set In Order, Shine, Standardize, and Sustain;
-
Kanban – visual signals like colored tape, stickers or other visual cues are used to keep track inventory.
-
Theory of Constraints - Identify bottlenecks in the process, and eliminate them using lean tools such kanban boards.
-
Just-in-time delivery - Deliver components and materials right to your point of use.
-
Continuous improvement - Make incremental improvements rather than overhauling the entire process.